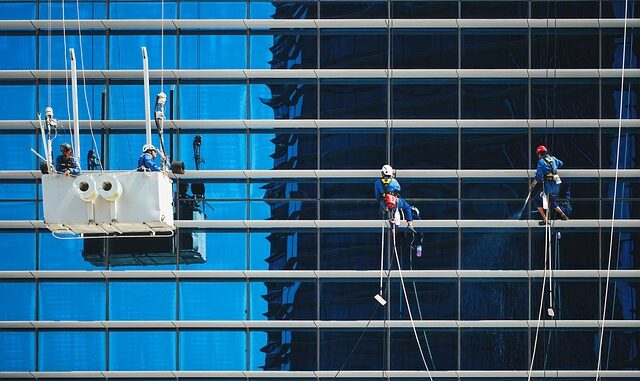
Abstract
This research report examines the multifaceted evolution of maintenance strategies, moving beyond the now-established concept of predictive maintenance (PdM) to explore emerging paradigms and their implications across diverse industries. While PdM, particularly when powered by Artificial Intelligence (AI), has demonstrated significant value, the report argues for a more holistic perspective encompassing advanced diagnostics, proactive maintenance, prescriptive maintenance, and the burgeoning field of autonomous maintenance. We analyze the core technologies underpinning these approaches, including advanced sensor networks, AI algorithms (time series analysis, machine learning, deep learning), digital twins, and the Industrial Internet of Things (IIoT). Furthermore, we investigate the challenges associated with implementation, data management, cybersecurity, and the crucial need for human-machine collaboration. The report critically evaluates the return on investment (ROI) for various strategies, considering both tangible cost savings and intangible benefits such as improved safety, reduced downtime, and enhanced operational efficiency. Finally, we propose future research directions, emphasizing the need for standardized frameworks, explainable AI (XAI), and the development of maintenance strategies that are not only predictive but also resilient and adaptive to dynamic operating environments.
Many thanks to our sponsor Esdebe who helped us prepare this research report.
1. Introduction
Maintenance, traditionally viewed as a necessary evil and a cost center, has undergone a dramatic transformation in recent decades. The evolution from reactive maintenance (run-to-failure) to preventive maintenance (time-based or usage-based) paved the way for the more sophisticated approach of predictive maintenance (PdM). PdM, driven by advanced sensor technologies and data analytics, aims to predict equipment failures before they occur, allowing for proactive intervention and minimizing downtime. The advent of Artificial Intelligence (AI), particularly machine learning (ML) and deep learning (DL), has further enhanced the capabilities of PdM, enabling more accurate predictions and the automation of maintenance tasks.
However, the narrative of maintenance evolution is far from complete. While PdM represents a significant advancement, it is not a panacea. The real-world effectiveness of PdM hinges on several factors, including the quality and quantity of data, the accuracy of the predictive models, and the seamless integration of maintenance activities with overall operational strategies. Moreover, PdM often focuses on predicting specific failure modes, neglecting the broader context of system health and performance optimization.
This report argues for a more comprehensive and forward-looking perspective on maintenance strategies. We contend that the future of maintenance lies in a synergistic approach that combines the strengths of PdM with other advanced techniques, such as proactive maintenance, prescriptive maintenance, and autonomous maintenance. We also emphasize the importance of addressing the challenges associated with data management, cybersecurity, and the integration of AI-driven systems with existing maintenance workflows.
Many thanks to our sponsor Esdebe who helped us prepare this research report.
2. From Reactive to Predictive: A Historical Overview
The journey of maintenance management can be characterized by a gradual shift from reactive, failure-based approaches to more proactive, condition-based methodologies. Each stage represents an attempt to minimize downtime, reduce costs, and improve overall operational efficiency.
- Reactive Maintenance (Run-to-Failure): This is the most basic and arguably least efficient approach. Maintenance is only performed after a failure has occurred. While seemingly cost-effective in the short term, it often leads to unplanned downtime, increased repair costs, and potential safety hazards. This strategy is generally suitable only for non-critical assets where the cost of failure is minimal.
- Preventive Maintenance (Time-Based/Usage-Based): Preventive maintenance involves performing maintenance tasks at predetermined intervals, regardless of the actual condition of the equipment. This approach aims to prevent failures by replacing or overhauling components before they reach the end of their expected lifespan. While preventive maintenance can reduce the likelihood of unexpected failures, it often results in unnecessary maintenance and wasted resources, as components are replaced even if they are still in good working order.
- Condition-Based Maintenance (CBM): CBM relies on monitoring the condition of equipment using various sensors and diagnostic techniques. Maintenance is performed only when there is evidence of impending failure. CBM offers a significant improvement over preventive maintenance by reducing unnecessary maintenance and allowing for more targeted interventions. However, the effectiveness of CBM depends on the accuracy and reliability of the monitoring equipment and the ability to interpret the data correctly.
- Predictive Maintenance (PdM): PdM builds upon CBM by using advanced data analytics and machine learning techniques to predict the remaining useful life (RUL) of equipment. This allows maintenance teams to schedule maintenance activities in advance, minimizing downtime and optimizing resource allocation. PdM is often considered the most advanced form of maintenance management, but it requires significant investment in sensors, data infrastructure, and skilled personnel.
Many thanks to our sponsor Esdebe who helped us prepare this research report.
3. The Role of Artificial Intelligence in Predictive Maintenance
AI, particularly machine learning and deep learning, has revolutionized PdM by enabling more accurate predictions, automated diagnostics, and optimized maintenance schedules. Several AI algorithms are commonly used in PdM applications:
- Time Series Analysis: Techniques such as ARIMA (Autoregressive Integrated Moving Average) and Kalman filtering are used to analyze time-dependent data, such as vibration signals, temperature readings, and pressure measurements. These algorithms can identify trends, patterns, and anomalies that may indicate impending failure. Time series analysis is particularly useful for predicting the RUL of equipment based on historical performance data.
- Machine Learning (ML): ML algorithms, such as support vector machines (SVMs), decision trees, and random forests, are used to classify equipment health and predict failures based on a variety of input features. ML models can be trained on historical data to identify complex relationships between sensor data and equipment performance. Supervised learning approaches are prevalent, requiring labeled data indicating past failures. Unsupervised learning can also be beneficial for anomaly detection and identifying novel failure modes.
- Deep Learning (DL): DL algorithms, such as convolutional neural networks (CNNs) and recurrent neural networks (RNNs), are capable of learning complex patterns from large datasets without explicit feature engineering. CNNs are commonly used for image and signal processing, while RNNs are particularly well-suited for analyzing sequential data, such as time series data. DL models can achieve higher accuracy than traditional ML models, but they require significantly more data and computational resources. Transfer learning strategies, where models pre-trained on large datasets are fine-tuned for specific maintenance tasks, are becoming increasingly popular.
- Reinforcement Learning (RL): While less common than other AI approaches, RL is emerging as a promising technique for optimizing maintenance schedules and resource allocation. RL agents can learn to make optimal decisions by interacting with a simulated environment, such as a digital twin of the equipment. This allows for the development of adaptive maintenance strategies that respond to changing operating conditions.
The effectiveness of AI-driven PdM depends on the quality and quantity of data used to train the models. Data preprocessing, feature engineering, and model validation are crucial steps in the development of robust and reliable predictive models. Furthermore, explainable AI (XAI) is becoming increasingly important, as it allows maintenance personnel to understand the reasoning behind the AI’s predictions and make informed decisions.
Many thanks to our sponsor Esdebe who helped us prepare this research report.
4. Advanced Sensor Technologies for Condition Monitoring
The success of PdM relies heavily on the availability of accurate and reliable sensor data. A wide range of sensors are used to monitor the condition of equipment, including:
- Vibration Sensors: Accelerometers and vibration probes are used to measure the vibration levels of rotating equipment, such as motors, pumps, and turbines. Changes in vibration patterns can indicate bearing wear, misalignment, imbalance, and other mechanical faults.
- Temperature Sensors: Thermocouples, resistance temperature detectors (RTDs), and infrared cameras are used to measure the temperature of equipment components. Elevated temperatures can indicate overheating, friction, and other problems.
- Pressure Sensors: Pressure transducers are used to measure the pressure of fluids in hydraulic and pneumatic systems. Changes in pressure can indicate leaks, blockages, and other system malfunctions.
- Acoustic Sensors: Microphones and ultrasonic sensors are used to detect abnormal sounds and vibrations that may indicate impending failure. Acoustic emission sensors are particularly sensitive to crack propagation and other microscopic defects.
- Oil Analysis Sensors: Online oil analysis sensors are used to monitor the condition of lubricating oil in real-time. These sensors can detect changes in viscosity, water content, particle contamination, and other parameters that can indicate wear and degradation.
- Current and Voltage Sensors: These sensors are used to monitor the electrical characteristics of motors and other electrical equipment. Changes in current and voltage can indicate insulation breakdown, winding faults, and other electrical problems.
The choice of sensors depends on the specific equipment being monitored and the types of failures being targeted. Wireless sensor networks (WSNs) are becoming increasingly popular, as they offer greater flexibility and ease of deployment compared to traditional wired sensors. The rise of the Industrial Internet of Things (IIoT) has further accelerated the adoption of wireless sensors and cloud-based data analytics platforms.
Many thanks to our sponsor Esdebe who helped us prepare this research report.
5. Beyond Predictive: Proactive, Prescriptive, and Autonomous Maintenance
While PdM focuses on predicting failures, more advanced maintenance strategies aim to proactively prevent failures and optimize maintenance activities based on a holistic understanding of system health and performance.
- Proactive Maintenance: This approach goes beyond simply predicting failures and focuses on identifying and addressing the root causes of equipment problems. Proactive maintenance involves a combination of predictive maintenance techniques, root cause analysis, and design improvements. The goal is to eliminate the underlying factors that contribute to equipment failures, rather than simply reacting to the symptoms. For example, if vibration analysis reveals that a bearing is failing due to misalignment, proactive maintenance would involve correcting the alignment to prevent future bearing failures.
- Prescriptive Maintenance: Prescriptive maintenance takes PdM to the next level by not only predicting failures but also recommending specific actions to mitigate the risk of failure and optimize maintenance schedules. Prescriptive maintenance systems use AI and machine learning to analyze data from multiple sources, including sensors, maintenance records, and operational data, to generate personalized recommendations for maintenance activities. These recommendations may include adjusting operating parameters, replacing specific components, or performing specific maintenance tasks. Prescriptive maintenance can significantly improve maintenance efficiency and reduce downtime by ensuring that the right maintenance actions are performed at the right time.
- Autonomous Maintenance: This emerging paradigm envisions a future where maintenance tasks are performed autonomously by robots and other intelligent machines. Autonomous maintenance systems would be capable of self-diagnosing problems, performing repairs, and adjusting operating parameters without human intervention. This could significantly reduce the cost of maintenance and improve the availability of equipment, particularly in hazardous or remote environments. Autonomous maintenance is still in its early stages of development, but it holds significant promise for the future of maintenance management. The use of digital twins will be critical for autonomous maintenance, allowing algorithms to test procedures and predict outcomes.
Many thanks to our sponsor Esdebe who helped us prepare this research report.
6. Challenges and Considerations in Implementing Advanced Maintenance Strategies
Implementing advanced maintenance strategies, such as PdM, proactive maintenance, prescriptive maintenance, and autonomous maintenance, presents several challenges:
- Data Quality and Availability: The effectiveness of AI-driven maintenance strategies depends heavily on the quality and quantity of data used to train the models. Data must be accurate, reliable, and representative of the operating conditions of the equipment. Data cleansing, preprocessing, and feature engineering are crucial steps in the development of robust and reliable predictive models. Furthermore, data must be readily available and accessible to the AI algorithms. This requires a robust data infrastructure and data governance policies.
- Data Security and Privacy: The collection and analysis of data from equipment and systems raise concerns about data security and privacy. Maintenance data may contain sensitive information about operational processes, equipment performance, and employee activities. It is essential to implement robust security measures to protect data from unauthorized access, use, and disclosure. Furthermore, it is important to comply with all applicable data privacy regulations.
- Integration with Existing Systems: Integrating AI-driven maintenance systems with existing maintenance management systems (CMMS) and enterprise resource planning (ERP) systems can be challenging. These systems often use different data formats and communication protocols. Interoperability standards and APIs are needed to facilitate seamless data exchange and integration.
- Skills Gap: Implementing and maintaining advanced maintenance strategies requires a skilled workforce with expertise in data science, machine learning, sensor technologies, and maintenance engineering. There is a growing skills gap in these areas, which can hinder the adoption of advanced maintenance strategies. Training and education programs are needed to develop the skills required to implement and maintain these systems.
- Cost and ROI: The initial investment in sensors, data infrastructure, and AI algorithms can be significant. It is essential to carefully evaluate the return on investment (ROI) before implementing advanced maintenance strategies. The ROI should consider both tangible cost savings, such as reduced downtime and maintenance costs, and intangible benefits, such as improved safety and operational efficiency.
- Human-Machine Collaboration: AI-driven maintenance systems should be designed to augment human capabilities, not replace them. Maintenance personnel should be trained to interpret the AI’s predictions and recommendations and make informed decisions based on their expertise and experience. Human-machine collaboration is essential for ensuring the safe and effective operation of advanced maintenance systems.
Many thanks to our sponsor Esdebe who helped us prepare this research report.
7. ROI Analysis of AI-Driven Maintenance
The return on investment (ROI) for AI-driven maintenance strategies can be substantial, but it is important to carefully consider all the costs and benefits involved. Tangible benefits include:
- Reduced Downtime: By predicting failures before they occur, AI-driven maintenance can significantly reduce unplanned downtime. This can translate into significant cost savings in terms of lost production, idle labor, and equipment damage.
- Lower Maintenance Costs: AI-driven maintenance can optimize maintenance schedules and resource allocation, reducing unnecessary maintenance and extending the lifespan of equipment. This can lead to lower maintenance costs in terms of labor, parts, and materials.
- Improved Equipment Reliability: By identifying and addressing the root causes of equipment problems, AI-driven maintenance can improve the overall reliability of equipment. This can reduce the risk of unexpected failures and improve the long-term performance of assets.
- Extended Asset Lifespan: Early detection of faults and proactive intervention can extend the lifespan of critical assets, deferring costly replacements.
Intangible benefits include:
- Improved Safety: AI-driven maintenance can help prevent accidents and injuries by identifying and mitigating potential hazards. This can improve workplace safety and reduce the risk of liability.
- Enhanced Operational Efficiency: AI-driven maintenance can optimize operational processes and improve overall efficiency. This can lead to increased productivity, reduced waste, and improved profitability.
- Better Decision-Making: AI-driven maintenance provides maintenance personnel with valuable insights and recommendations, enabling them to make better decisions about maintenance activities. This can improve the effectiveness of maintenance operations and reduce the risk of errors.
- Improved Resource Allocation: Accurately predicting maintenance needs allows for optimised staffing and resource management, ensuring availability when needed.
However, it is important to note that the ROI for AI-driven maintenance can vary significantly depending on the specific application and the maturity of the maintenance program. It is essential to conduct a thorough cost-benefit analysis before implementing AI-driven maintenance to ensure that the investment is justified. The ROI can also be improved by focusing on high-value assets and critical equipment where the cost of failure is high.
Many thanks to our sponsor Esdebe who helped us prepare this research report.
8. Future Research Directions
The field of maintenance management is constantly evolving, and there are several promising areas for future research:
- Explainable AI (XAI): Developing XAI techniques that can explain the reasoning behind AI’s predictions and recommendations is crucial for building trust and acceptance of AI-driven maintenance systems. XAI can help maintenance personnel understand why the AI is recommending a particular action, allowing them to make informed decisions based on their expertise and experience.
- Federated Learning: Exploring federated learning techniques that allow AI models to be trained on distributed datasets without sharing sensitive data. This can enable the development of more robust and reliable predictive models while protecting data privacy.
- Digital Twin Technology: Integrating digital twin technology with AI-driven maintenance systems to create virtual representations of equipment and systems that can be used for simulation, training, and optimization. Digital twins can provide a more holistic view of equipment health and performance, enabling more accurate predictions and optimized maintenance schedules.
- Autonomous Maintenance Systems: Developing autonomous maintenance systems that can perform maintenance tasks without human intervention. This requires advances in robotics, computer vision, and AI. Research should focus on developing safe, reliable, and adaptable autonomous maintenance systems.
- Standardized Frameworks and Protocols: Establishing standardized frameworks and protocols for data exchange, communication, and interoperability between different maintenance systems. This can facilitate the integration of AI-driven maintenance systems with existing systems and promote the adoption of best practices.
- Resilient and Adaptive Maintenance Strategies: Developing maintenance strategies that are resilient to unexpected events and adaptive to changing operating conditions. This requires the development of AI algorithms that can learn from experience and adjust maintenance schedules in response to dynamic changes in the environment. The ability to manage uncertainty and adapt to unforeseen circumstances is essential for ensuring the long-term reliability and availability of equipment.
Many thanks to our sponsor Esdebe who helped us prepare this research report.
9. Conclusion
The evolution of maintenance strategies from reactive to predictive and beyond represents a significant advancement in asset management and operational efficiency. While predictive maintenance, particularly when augmented by AI, has demonstrated considerable value, it is crucial to recognize its limitations and embrace a more holistic approach. Proactive, prescriptive, and autonomous maintenance paradigms offer promising avenues for optimizing maintenance activities and minimizing downtime.
Successfully implementing these advanced strategies requires careful consideration of several factors, including data quality, security, system integration, and workforce skills. Furthermore, a thorough ROI analysis is essential to justify the investment and ensure that the benefits outweigh the costs. Future research should focus on developing explainable AI, federated learning techniques, digital twin technology, and standardized frameworks to further enhance the capabilities and adoption of advanced maintenance strategies.
Ultimately, the future of maintenance lies in a synergistic approach that combines the strengths of human expertise with the power of AI, creating resilient and adaptive maintenance systems that can ensure the long-term reliability, safety, and efficiency of critical assets.
Many thanks to our sponsor Esdebe who helped us prepare this research report.
References
- Lee, J., Lapira, E., Bagheri, B., & Kao, H. A. (2013). Recent advances and trends in predictive manufacturing systems in the big data era. International Journal of Production Research, 51(2), 405-418.
- Jardine, A. K. S., Lin, D., & Banjevic, D. (2006). A review on machinery diagnostics and prognostics implementing condition-based maintenance. Mechanical Systems and Signal Processing, 20(7), 1483-1510.
- Mobley, R. K. (2002). An introduction to predictive maintenance. Butterworth-Heinemann.
- Susto, G. A., Schirru, A., Pampuri, S., McLoone, S., & Beghi, A. (2015). Machine learning for predictive maintenance: A multiple classifier approach. IEEE Transactions on Industrial Informatics, 11(3), 814-822.
- Hines, J. W., & Garvey, P. M. (2010). Benchmarking of diagnostics and prognostics technology. Reliability Engineering & System Safety, 95(7), 766-777.
- Liu, R., Wang, B., Yang, L., & Wang, W. (2018). Remaining useful life prediction of rolling element bearings based on deep learning. IEEE Transactions on Industrial Electronics, 65(7), 5638-5647.
- Tao, F., Cheng, J., Qi, Q., Zhang, M., Zhang, H., & Sui, F. (2017). Digital twin-driven product design, manufacturing and service with big data. International Journal of Advanced Manufacturing Technology, 94(9-12), 3563-3576.
- Wuest, T., Weimer, D., Irgens, C., & Thoben, K. D. (2016). Machine learning in manufacturing: advantages, challenges, and applications. Production & Manufacturing Research, 4(1), 23-45.
- Goebel, K., Saha, B., Saxena, A., Celaya, J. R., & Christophersen, H. A. (2008). Prognostics in aerospace. IEEE Aerospace and Electronic Systems Magazine, 23(11), 4-15.
- Liao, H., Zhao, P., & Zhang, Z. (2006). Failure prognosis using wavelet neural network with immune algorithm for bearing health condition monitoring. Expert Systems with Applications, 31(1), 191-199.
The report highlights the importance of data quality for AI-driven maintenance. Expanding on this, what strategies can organizations employ to ensure data integrity and minimize biases in their datasets to improve predictive accuracy and reliability?
That’s a great point! Data integrity and bias are critical. We found that robust data governance frameworks, including automated validation checks and diverse data sourcing, are key. Encouraging collaboration between data scientists and domain experts helps identify and mitigate potential biases. What methods have you seen work well in practice?
Editor: MedTechNews.Uk
Thank you to our Sponsor Esdebe
The discussion of proactive maintenance as a method to address the root causes of equipment problems is insightful. How can organizations effectively integrate root cause analysis into their maintenance workflows to transition from reactive to truly proactive strategies?
That’s a key question! I think a crucial step is empowering maintenance teams to investigate beyond the immediate failure. Implementing a structured RCA process, perhaps using a framework like 5 Whys or a fishbone diagram, can help. Integrating this directly into the CMMS workflow ensures that root causes are documented and addressed, not just the symptoms. Has anyone seen success with specific RCA tools?
Editor: MedTechNews.Uk
Thank you to our Sponsor Esdebe
Autonomous maintenance? So, the robots will fix themselves now? I’m picturing tiny robot mechanics swarming over their larger brethren. Sounds like a sci-fi movie waiting to happen. What’s the timeline on Skynet…err, I mean, fully autonomous maintenance becoming a reality?
That’s a fun image! While tiny robot mechanics might be a while off, the idea of autonomous maintenance focuses on AI-driven systems that can diagnose and even perform simple repairs. Think of it as a stepping stone, automating routine tasks and freeing up human experts for complex issues. The timeline depends heavily on industry and application!
Editor: MedTechNews.Uk
Thank you to our Sponsor Esdebe