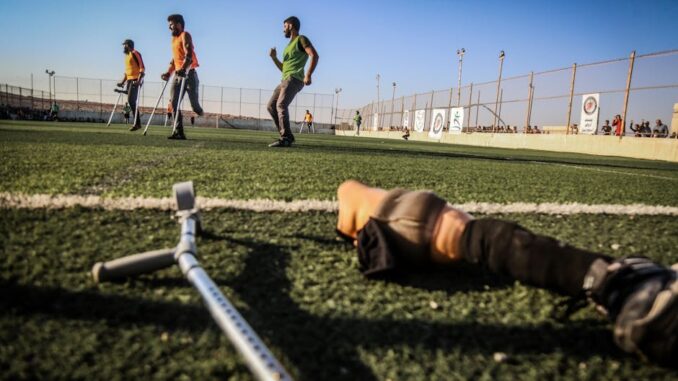
Abstract
Prosthetic technology has undergone significant advancements in recent decades, driven by innovations in materials science, robotics, neuroscience, and computer engineering. This report provides a comprehensive overview of the field, encompassing its historical evolution, current state-of-the-art prosthetic limbs, materials and manufacturing techniques, control mechanisms (with a particular focus on neural interfaces), the economic and accessibility challenges, and anticipated future trends. While the Phantom X neural interface represents a crucial step forward, this report contextualizes such advancements within the broader landscape of prosthetic research and development. We address the limitations of current technologies, emphasizing the need for improved sensory feedback, personalized design, robust control algorithms, and reduced cost to enhance the quality of life for amputees and individuals with limb differences. This review highlights both the remarkable progress and the remaining obstacles in realizing truly seamless and intuitive prosthetic integration.
Many thanks to our sponsor Esdebe who helped us prepare this research report.
1. Introduction
The field of prosthetics aims to restore lost function and improve the quality of life for individuals who have experienced limb loss or have congenital limb deficiencies. Amputation, resulting from trauma, disease (such as diabetes or peripheral vascular disease), or congenital conditions, presents a significant physical and psychological challenge. Prosthetic limbs are designed to replace missing limbs, providing support, mobility, and a degree of functional restoration. This report provides a broad examination of the prosthetic field, tracing its history, analyzing current technologies, and speculating on future directions.
The development of prosthetics is a multidisciplinary endeavor, drawing from engineering, materials science, neuroscience, and rehabilitation medicine. Early prosthetic devices were primarily focused on basic functionality, such as providing a stable base for walking. However, advancements in technology have enabled the development of increasingly sophisticated prosthetics that offer improved dexterity, control, and cosmetic appearance. While significant strides have been made, several challenges remain, including achieving seamless integration with the user’s nervous system, providing adequate sensory feedback, reducing the weight and cost of devices, and ensuring accessibility for all individuals who need them. This report will analyze each of these aspects in detail.
Many thanks to our sponsor Esdebe who helped us prepare this research report.
2. Historical Perspective
The history of prosthetics dates back to ancient times. Evidence suggests that rudimentary prosthetics were used in ancient Egypt and Rome. These early devices were primarily made of wood, leather, and metal, and their function was limited to providing basic support and mobility. The creation of the Roman Capua leg around 300 BC is often cited as an early example of a prosthetic device. Over the centuries, prosthetic design evolved gradually, with improvements in materials and construction techniques.
The Renaissance period saw the development of more sophisticated prosthetic limbs, including articulated hands and legs. Ambroise Paré, a French surgeon, made significant contributions to prosthetic design in the 16th century, including the invention of articulated prostheses and locking knee joints. However, widespread adoption of these more advanced devices remained limited due to cost and manufacturing constraints.
The American Civil War led to a surge in demand for prosthetic limbs. This prompted further innovation in design and manufacturing. James Hanger, a Confederate soldier who lost his leg in battle, developed the “Hanger Limb,” which became a popular prosthetic design. Mass production techniques were introduced, making prosthetics more accessible to a larger number of individuals.
In the 20th century, significant advancements were made in prosthetic technology, driven by wartime needs and technological breakthroughs. The development of lightweight and durable materials, such as aluminum and plastics, led to improved prosthetic designs. Myoelectric prosthetics, which are controlled by electrical signals generated by muscles, were introduced in the 1960s, offering a more natural and intuitive control mechanism.
Many thanks to our sponsor Esdebe who helped us prepare this research report.
3. Current State-of-the-Art Prosthetic Limbs
Modern prosthetic limbs represent a significant leap forward from their historical counterparts. They incorporate advanced materials, sophisticated control mechanisms, and personalized design features. Current state-of-the-art prosthetics can be broadly classified into the following categories:
- Conventional Prosthetics: These are the most basic type of prosthetics, typically consisting of a socket that attaches to the residual limb, a pylon that provides structural support, and a terminal device (e.g., a prosthetic foot or hand). Conventional prosthetics are relatively inexpensive and durable, but they offer limited functionality and control. They are often body-powered, meaning they rely on harnesses and cables to transmit movement from the user’s body to the terminal device.
- Myoelectric Prosthetics: Myoelectric prosthetics utilize electromyography (EMG) signals generated by muscles in the residual limb to control the movement of the prosthetic limb. Electrodes placed on the skin detect these signals, which are then processed by a microprocessor to control motors that move the prosthetic joints. Myoelectric prosthetics offer more intuitive control compared to conventional prosthetics, but they are more expensive and require specialized training to use effectively.
- Hybrid Prosthetics: Hybrid prosthetics combine features of both conventional and myoelectric prosthetics. For example, a hybrid upper limb prosthesis might use a body-powered harness to control the elbow joint and myoelectric control for the hand. This approach can provide a balance between functionality, control, and cost.
- Microprocessor-Controlled Prosthetics: These prosthetics use sophisticated microprocessors and sensors to monitor the user’s movements and adjust the prosthetic limb accordingly. Microprocessor-controlled prosthetic knees, for example, can adjust the resistance of the knee joint in real-time to provide greater stability and control during walking. These devices offer significant improvements in gait symmetry and reduce the risk of falls.
- Osseointegrated Prosthetics: Osseointegration involves surgically implanting a prosthetic attachment directly into the bone of the residual limb. This allows for a more direct and stable connection between the prosthetic limb and the user’s body, eliminating the need for a socket. Osseointegration can improve proprioception, reduce skin irritation, and enhance comfort, but it also carries a higher risk of infection and requires a longer recovery period.
The sophistication of available prosthetics varies greatly, with some designs offering highly advanced features. Research is constantly ongoing to refine these current technologies and explore new avenues for improving prosthetic function and usability. However, the cost, complexity, and training requirements associated with many advanced prosthetics can limit their accessibility to a broader population.
Many thanks to our sponsor Esdebe who helped us prepare this research report.
4. Materials and Manufacturing Techniques
The materials used in prosthetic limbs play a crucial role in their weight, durability, and functionality. Modern prosthetics utilize a wide range of materials, including:
- Metals: Aluminum, titanium, and stainless steel are commonly used for structural components, such as pylons and joint mechanisms. These materials offer high strength and durability.
- Plastics: Thermoplastics (e.g., polypropylene, polyethylene) and thermosetting plastics (e.g., carbon fiber reinforced polymers) are used for sockets, cosmetic covers, and other components. Plastics offer a good balance of strength, weight, and cost. Carbon fiber composites are particularly popular due to their high strength-to-weight ratio.
- Elastomers: Silicone, polyurethane, and other elastomers are used for liners, cushions, and cosmetic coverings. Elastomers provide cushioning and comfort, and they can be molded to resemble natural skin.
- Smart Materials: Shape memory alloys (SMAs) and electroactive polymers (EAPs) are being explored for use in prosthetic actuators and sensors. These materials can change their shape or stiffness in response to external stimuli, enabling the development of more compact and energy-efficient prosthetic devices.
Manufacturing techniques for prosthetic limbs have also evolved significantly. Traditional methods, such as hand-crafting and machining, are still used for some components, but increasingly sophisticated techniques are being employed.
- Computer-Aided Design (CAD) and Computer-Aided Manufacturing (CAM): CAD/CAM technology allows for the creation of custom prosthetic designs based on precise measurements of the residual limb. This enables the fabrication of sockets that fit comfortably and provide optimal support.
- 3D Printing (Additive Manufacturing): 3D printing is revolutionizing the manufacturing of prosthetic limbs. It allows for the creation of complex geometries and customized designs with relatively low cost and lead time. 3D-printed sockets, hands, and other components are becoming increasingly common.
- Robotic Manufacturing: Robotic manufacturing techniques are being used to automate the production of prosthetic components, improving precision and efficiency. This can lead to lower manufacturing costs and faster turnaround times.
These advances in materials and manufacturing are crucial for creating prosthetics that are lighter, stronger, more comfortable, and more affordable. The adoption of 3D printing, in particular, has the potential to democratize access to prosthetic technology by enabling the creation of customized devices at a fraction of the cost of traditional methods. However, quality control and regulatory considerations remain important challenges in the widespread adoption of 3D-printed prosthetics.
Many thanks to our sponsor Esdebe who helped us prepare this research report.
5. Control Mechanisms
The control mechanism is a critical aspect of prosthetic limb design, as it determines how the user interacts with and controls the device. Various control mechanisms are used in modern prosthetics, each with its own advantages and disadvantages.
- Body-Powered Control: As mentioned previously, body-powered prosthetics rely on harnesses and cables to transmit movement from the user’s body to the prosthetic limb. For example, shoulder abduction can be used to control the opening and closing of a prosthetic hand. Body-powered prosthetics are relatively simple and durable, but they require significant physical effort and provide limited dexterity.
- Myoelectric Control: Myoelectric control uses EMG signals generated by muscles in the residual limb to control the movement of the prosthetic limb. Electrodes placed on the skin detect these signals, which are then processed by a microprocessor to control motors that move the prosthetic joints. Myoelectric control offers more intuitive control compared to body-powered control, but it requires specialized training and can be affected by muscle fatigue and sweating.
- Pattern Recognition Control: Pattern recognition control is an advanced form of myoelectric control that uses machine learning algorithms to recognize patterns in EMG signals. This allows for more complex and coordinated movements to be controlled by the user. For example, a user might be able to perform a grasping motion by simply thinking about it, without having to consciously contract specific muscles.
- Targeted Muscle Reinnervation (TMR): TMR is a surgical procedure that involves transferring nerves from the amputated limb to other muscles in the body. This allows for more EMG signals to be available for controlling the prosthetic limb, improving dexterity and control. TMR is often combined with pattern recognition control to further enhance functionality.
- Neural Interfaces: Neural interfaces represent the most advanced control mechanism for prosthetic limbs. These interfaces directly connect to the user’s nervous system, allowing for even more intuitive and precise control. Neural interfaces can be either invasive (requiring surgical implantation) or non-invasive (using electrodes placed on the scalp). Examples of neural interfaces include:
- Electrocorticography (ECoG): ECoG involves placing electrodes on the surface of the brain to record electrical activity. This provides a more direct and stable signal compared to EEG, but it requires a surgical procedure.
- Intracortical Microelectrode Arrays (ICMAs): ICMAs involve implanting arrays of microelectrodes directly into the motor cortex of the brain. This provides the most direct and precise control over prosthetic limbs, but it also carries the highest risk of complications.
- The Phantom X Neural Interface: The Phantom X, as mentioned in the prompt, represents a significant advancement in neural interface technology. The specific details of Phantom X would require further research beyond the prompt itself. However, such an interface likely aims to improve signal quality, stability, and longevity compared to existing neural interfaces.
Neural interfaces hold immense promise for restoring natural movement and sensation to amputees. However, significant challenges remain, including biocompatibility, signal stability, long-term reliability, and ethical considerations. The Phantom X interface, if successful, would contribute to overcoming these limitations and pave the way for more widespread adoption of neural-controlled prosthetics.
Many thanks to our sponsor Esdebe who helped us prepare this research report.
6. Sensory Feedback
One of the most significant limitations of current prosthetic limbs is the lack of sensory feedback. Amputees typically rely on visual cues and proprioception from the residual limb to control their prosthetic limb. This can make it difficult to perform delicate tasks and can lead to fatigue and frustration. Restoring sensory feedback is a major goal in prosthetic research.
Various approaches are being explored to provide sensory feedback to amputees:
- Vibration Feedback: Vibration motors can be used to provide tactile feedback, such as indicating the amount of force being applied by a prosthetic hand. This type of feedback is relatively simple to implement, but it provides limited information.
- Electrical Stimulation: Electrical stimulation can be used to stimulate sensory nerves in the residual limb, creating the sensation of touch or pressure. This can provide more realistic sensory feedback compared to vibration feedback.
- Targeted Sensory Reinnervation (TSR): TSR is a surgical procedure that involves transferring sensory nerves from the amputated limb to the skin of the chest or upper arm. This creates a “sensory map” on the skin that corresponds to different parts of the prosthetic limb. When the prosthetic limb touches an object, the corresponding area of the skin on the chest or arm is stimulated, providing sensory feedback.
- Cortical Stimulation: Direct stimulation of the somatosensory cortex of the brain can be used to create realistic sensations of touch, pressure, and temperature. This approach holds great promise for restoring natural sensation to amputees, but it requires invasive surgery and careful calibration.
While significant progress has been made in restoring sensory feedback, several challenges remain. These include developing reliable and biocompatible stimulation techniques, creating realistic and informative sensory experiences, and integrating sensory feedback into the control loop of the prosthetic limb. The ability to provide amputees with realistic and intuitive sensory feedback would significantly enhance their ability to control and use their prosthetic limbs.
Many thanks to our sponsor Esdebe who helped us prepare this research report.
7. Cost and Accessibility
The cost of prosthetic limbs is a significant barrier to access for many individuals who need them. Advanced prosthetic limbs, such as myoelectric and microprocessor-controlled prosthetics, can cost tens of thousands of dollars or more. This cost can be prohibitive for individuals with limited financial resources or inadequate insurance coverage.
In addition to the initial cost of the prosthetic limb, there are ongoing costs associated with maintenance, repairs, and replacement. Prosthetic limbs typically have a limited lifespan and require periodic maintenance to ensure proper function. The socket, in particular, often needs to be replaced due to changes in the volume of the residual limb.
The accessibility of prosthetic limbs is also affected by factors such as geographic location and availability of qualified prosthetists. In some areas, particularly in developing countries, there may be a shortage of trained prosthetists and limited access to prosthetic services. This can make it difficult for individuals to obtain the prosthetic limbs they need.
Efforts are being made to reduce the cost and improve the accessibility of prosthetic limbs. These include:
- Developing more affordable prosthetic designs: Researchers are working on developing simpler and more cost-effective prosthetic designs that still provide adequate functionality.
- Using 3D printing to reduce manufacturing costs: As mentioned previously, 3D printing can significantly reduce the cost of manufacturing prosthetic limbs.
- Providing financial assistance to amputees: Government agencies and non-profit organizations offer financial assistance to help amputees pay for prosthetic limbs.
- Training more prosthetists: Efforts are being made to train more prosthetists, particularly in underserved areas.
- Promoting international collaborations: International collaborations can help to share knowledge and resources and improve access to prosthetic limbs in developing countries.
Addressing the cost and accessibility barriers is crucial to ensuring that all individuals who need prosthetic limbs have access to them. This requires a multi-faceted approach involving technological innovation, policy changes, and increased financial support.
Many thanks to our sponsor Esdebe who helped us prepare this research report.
8. Future Trends
The field of prosthetics is rapidly evolving, driven by advancements in technology and a growing understanding of the human body. Several future trends are expected to shape the field in the coming years.
- Advanced Robotics: Future prosthetic limbs will likely incorporate more advanced robotics, enabling more complex and coordinated movements. This will involve the use of more sophisticated actuators, sensors, and control algorithms.
- Brain-Computer Interfaces (BCIs): BCIs hold immense promise for providing even more intuitive and precise control over prosthetic limbs. Future BCIs will likely be less invasive and more reliable, allowing amputees to control their prosthetic limbs with their thoughts.
- Sensory Augmentation: Future prosthetic limbs will likely provide more realistic and informative sensory feedback, allowing amputees to experience the world in a more natural way. This will involve the use of advanced stimulation techniques and sophisticated sensory processing algorithms.
- Personalized Prosthetic Design: Future prosthetic limbs will be increasingly customized to meet the individual needs and preferences of each user. This will involve the use of advanced CAD/CAM technology and 3D printing to create prosthetics that fit perfectly and provide optimal functionality.
- Regenerative Medicine: In the long term, regenerative medicine techniques may be able to regenerate lost limbs, eliminating the need for prosthetic limbs altogether. While this is still a distant goal, research in this area is progressing rapidly.
- AI and Machine Learning: AI and machine learning will play an increasingly important role in prosthetic design and control. AI algorithms can be used to optimize prosthetic designs, personalize control strategies, and provide real-time assistance to users.
- Improved Biocompatibility: Future prosthetic materials will be more biocompatible, reducing the risk of inflammation and rejection. This will involve the use of advanced materials and surface treatments.
These future trends hold the potential to transform the field of prosthetics and significantly improve the lives of amputees. Continued research and development in these areas are crucial to realizing this potential.
Many thanks to our sponsor Esdebe who helped us prepare this research report.
9. Conclusion
Prosthetic technology has made remarkable progress in recent decades, offering individuals with limb loss or limb differences increasingly sophisticated and functional solutions. From the rudimentary devices of ancient times to the advanced myoelectric and neural-controlled prosthetics of today, the field has continuously evolved to meet the needs of its users. While current state-of-the-art prosthetics offer significant improvements in mobility, dexterity, and quality of life, several challenges remain. These include the lack of adequate sensory feedback, the high cost and limited accessibility of advanced devices, and the need for more robust and intuitive control mechanisms.
Future trends in prosthetic technology, such as advanced robotics, brain-computer interfaces, sensory augmentation, personalized design, and regenerative medicine, hold immense promise for further improving the lives of amputees. Continued research and development in these areas, coupled with efforts to reduce costs and improve accessibility, are crucial to realizing the full potential of prosthetic technology.
Ultimately, the goal of prosthetic research and development is to create prosthetic limbs that are seamlessly integrated with the user’s body and mind, allowing them to live full and active lives without limitations. While this is a challenging goal, the remarkable progress that has been made to date suggests that it is within reach.
Many thanks to our sponsor Esdebe who helped us prepare this research report.
References
- Aszmann, O. C., Ditting, T., Gabl, M., Götz, W., Hofer, C., Hussl, H., … & Salminger, S. (2015). Bionic reconstruction of the upper extremity with osseointegration, targeted muscle reinnervation, and pattern recognition. Plastic and Reconstructive Surgery, 135(5), 1231-1239.
- Atkins, D. J., & Heard, D. C. (2008). Upper-limb prosthetics: current developments and challenges. Journal of Hand Surgery, 33(9), 1620-1635.
- Bensmaia, S. J., & Miller, L. E. (2014). Restoring sensorimotor function through intracortical interfaces: progress and challenges. Nature Neuroscience, 17(3), 313-320.
- Chadwell, A., Kenney, L., & Granat, M. (2016). Myoelectric control of upper limb prostheses: advancements, challenges, and future directions. Expert Review of Medical Devices, 13(11), 1003-1011.
- Childress, D. S. (1985). Historical aspects of powered limb prostheses. Clinical Prosthetics and Orthotics, 9(1), 2-13.
- Cipriani, C., Carrozza, M. C., & Edin, B. B. (2011). Restoring natural sensory feedback in real-time bidirectional hand prostheses. Journal of Neuroengineering and Rehabilitation, 8(1), 29.
- Heger, H., & Billings, L. (1976). Knee stability in above-knee prostheses. Orthotics and Prosthetics, 30(1), 17-25.
- Herr, H. M. (2009). Exoskeletons and orthoses: classification, design challenges and future directions. Journal of Neuroengineering and Rehabilitation, 6(1), 21.
- Kuiken, T. A., Dumanian, G. A., Lipschutz, R. D., Miller, L. A., & Stubblefield, K. A. (2009). Targeted reinnervation for enhanced prosthetic arm function. Annals of the New York Academy of Sciences, 1170(1), 305-312.
- Resnik, L., Borgia, M., Pipitone, D. N., & Dislaire, R. (2013). Clinical outcomes of targeted muscle reinnervation for upper limb amputees: a systematic review. Journal of Rehabilitation Research and Development, 50(4), 487-502.
- Shepherd, D. E. T. (2015). 3D printing of prosthetic devices: Opportunities and challenges. Journal of Prosthetics and Orthotics, 27(3), 87-95.
So, Esdebe helped prepare the report, huh? Guessing seamless integration with the nervous system costs extra, and “accessibility” just means they’ll sell you the slightly-less-fancy model. Still, good to know my future SkyNet overlords will be ethically sponsored.
That’s a funny take! You’re right, accessibility is a huge challenge. We’re hoping advancements push costs down and make sophisticated prosthetics more widely available. Ethical considerations are definitely top-of-mind as the tech advances. It will be important to keep those discussions going as things progress!
Editor: MedTechNews.Uk
Thank you to our Sponsor Esdebe
“Seamless integration” sounds promising, but will these future limbs come with a built-in obsolescence plan? I mean, what happens when Esdebe releases the “Prosthetic 2.0” and suddenly my perfectly good bionic arm is considered vintage? Asking for a friend… who may or may not need a hand.
That’s a great point! The idea of planned obsolescence is definitely something worth considering as technology advances. We hope future prosthetic development focuses on upgradability and adaptability, ensuring users can benefit from new features without needing a complete replacement. Thanks for raising this important question!
Editor: MedTechNews.Uk
Thank you to our Sponsor Esdebe
The overview of control mechanisms is fascinating, particularly the neural interfaces. It would be interesting to explore the potential for non-invasive neural interfaces, like advanced EEG techniques, to provide a more accessible alternative to surgical implants for prosthetic control.