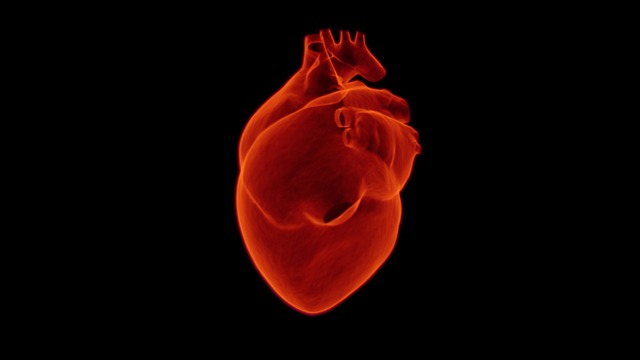
Micro Moulding: Precision’s Tiny Footprint Revolutionizing Medical Technology
You know, in the grand, ever-accelerating race of medical innovation, there are certain technological breakthroughs that don’t just move the needle; they redefine the entire playing field. Micro moulding, my friends, is absolutely one of them. It’s truly incredible what engineers are achieving now, producing miniature, unbelievably intricate components with precision levels that, honestly, were science fiction just a couple of decades ago.
This isn’t merely a technical feat, you see. It’s a fundamental shift in how we approach the very core of medical device design and manufacturing, ushering in an era of solutions that are not only more effective but also remarkably patient-friendly. We’re talking about devices that integrate seamlessly with the human body, facilitating less invasive procedures and dramatically improving diagnostic accuracy. It’s a transformation driven by the ability to craft the impossibly small with unflinching accuracy, and it’s making a profound impact across the entire healthcare spectrum.
Safeguard patient information with TrueNASs self-healing data technology.
The Unflinching Demand for Precision in Medical Device Manufacturing
Imagine, for a moment, a surgeon performing a delicate neurovascular procedure, navigating the brain’s incredibly fine arterial network. Or perhaps a cardiologist implanting a stent into a coronary artery, each movement a precise dance between skill and technology. In these critical moments, the instruments and implants simply cannot fail, can they? They demand absolute, unwavering precision, and that’s precisely where micro moulding steps onto the stage, a true protagonist in this high-stakes drama.
This technology allows us to create components with tolerances that are almost mind-bogglingly tight, often as low as +/-0.001mm. Just think about that for a second. We’re talking about a deviation thinner than a human hair, sometimes even an atom or two, in components that are themselves barely visible to the naked eye. This kind of exacting accuracy is absolutely non-negotiable for devices like advanced catheters, next-generation stents, and the ultra-fine tips of surgical tools. Any deviation, even the slightest miscalculation in form or fit, could lead to dire complications, compromising efficacy, or worse, patient safety.
Take, for instance, the evolution of cannulas. I recently heard about a company pushing the boundaries, developing a process to produce thin-walled cannulas where the wall thickness measures a mere 0.004 inches (that’s about 0.1016 mm). This isn’t just a number; it’s a game-changer for device reliability and performance, allowing for increased lumen size in a smaller overall footprint, facilitating smoother navigation through vascular pathways.
When you dive deeper into specific medical applications, the necessity of this precision becomes even more apparent. In ophthalmology, for example, the tiny components used in glaucoma shunts or intraocular lenses require flawless dimensions to ensure proper fluid drainage and optical clarity. For drug-eluting stents, the precise thickness and uniformity of the polymer coating, often containing the active pharmaceutical ingredient, are paramount for controlled drug release. Get it wrong, and you’re compromising the therapeutic window. Even in orthopaedics, where you might think bigness matters, micro-moulded components within complex joint replacement mechanisms, like tiny stops or guides, ensure smooth, frictionless movement and longevity. It’s all about reducing friction, preventing wear, and ensuring decades of reliable function.
Moreover, this level of precision isn’t just about the external dimensions. It extends to the internal geometries, the surface finishes, and even the molecular integrity of the materials themselves. Think about the micro-textures engineered onto implant surfaces to encourage tissue ingrowth or the microscopic channels within a sensor that need to be absolutely free of burrs or defects to ensure accurate readings. Micro moulding delivers this consistent quality, component after component, batch after batch. It truly elevates what’s possible, doesn’t it?
Revolutionizing Drug Delivery Systems through Miniaturization
Now, let’s pivot to the realm of drug delivery, an area where innovation directly translates to better patient outcomes and, frankly, a lot less hassle. Traditionally, manufacturing many drug delivery components often involved a complex dance of multiple separate steps: extrusion of tubes, tipping them, then perhaps gluing various parts together. Each step, you see, introduces potential points of failure, increasing the risk of contamination, misalignment, or just plain old manufacturing errors. It’s a logistical headache, and it’s less reliable for patients.
This is where micro moulding flexes its muscles, offering a vastly superior approach. By integrating complex geometries and features into a single, monolithic component, manufacturers can produce sophisticated drug delivery devices in one go. Imagine eliminating the need for separate extrusion, tipping, and gluing steps entirely. The benefits are multifold: it dramatically streamlines production workflows, slashes assembly costs, and, critically, vastly improves the consistency and safety of these vital systems. You end up with a higher quality, more reliable product hitting the market, and patients get the consistent dosages they need.
Consider the rise of micro-needle arrays for painless drug delivery or continuous glucose monitoring. These tiny structures, often just tens or hundreds of microns long, are perfectly formed by micro moulding, ensuring precise penetration depth and drug release kinetics. Or think about components for sophisticated inhalers; micro moulding ensures the intricate internal pathways and tiny orifices are perfectly formed for consistent aerosol delivery, which is absolutely vital for patients with respiratory conditions. It’s about ensuring every puff delivers exactly what’s prescribed.
This technology also plays a crucial role in enabling targeted and sustained drug release. Small, implantable drug reservoirs or osmotic pumps, precisely moulded to release medication over days, weeks, or even months, are becoming a reality. This reduces the burden of daily pill regimens, improves patient compliance, and can lead to more consistent therapeutic levels in the bloodstream. For chronic conditions, this is a monumental improvement in quality of life. Wouldn’t you agree that convenience combined with efficacy is a powerful combination for patients?
Unlocking Innovation in Implantable Devices
Implantable devices, those silent workhorses within our bodies, have undergone a truly remarkable transformation thanks to the advent of micro moulding. From life-sustaining pacemakers and defibrillators to sophisticated neurostimulation devices and advanced orthopaedic implants, the ability to create smaller, more complex components has had a cascading positive effect. Think about it: smaller devices often mean less invasive surgical procedures, which in turn leads to shorter hospital stays, reduced pain, and significantly faster recovery times for patients. It’s a win-win situation all around.
Consider the evolution of cardiac rhythm management devices. Years ago, they were comparatively bulky. Now, thanks to miniaturized connectors, intricate sensor housings, and delicate circuit board encapsulations, all enabled by micro moulding, these devices are becoming progressively smaller and more refined, making implantation less traumatic. Similarly, in the burgeoning field of neural interfaces, tiny electrodes and leads that connect directly to the brain or spinal cord rely entirely on the precision and minute scale that micro moulding provides. These aren’t just smaller versions of old tech; they are fundamentally new capabilities unlocked by the ability to mould on a micro scale.
Perhaps one of the most exciting frontiers in implantable technology, significantly facilitated by micro moulding, is the integration of biodegradable materials. Imagine an implant designed to support healing, then simply dissolving naturally within the body once its job is done. This eliminates the need for subsequent removal surgeries, reducing patient burden and healthcare costs. Materials like polylactic-co-glycolic acid (PLGA) or polycaprolactone (PCL) can be precisely moulded into scaffolds, drug-eluting implants, or temporary fixation devices. The trick, though, isn’t just moulding them; it’s moulding them with the precise microstructure to control their degradation rate and mechanical properties within the body. It’s a delicate balance of material science and manufacturing prowess.
However, working with these biocompatible and biodegradable polymers isn’t without its challenges. They often have very specific processing windows; too much heat or pressure, and you can alter their molecular structure, affecting their degradation profile or mechanical strength. This is where the meticulous process control of micro moulding truly shines, allowing for the gentle yet precise handling of these sensitive materials, ensuring the final implant performs exactly as intended for its lifespan, however long or short that may be. This isn’t just about making something small; it’s about making something small and perfectly functional for its intended biological environment. And that, my friends, is a huge step forward for patient care.
Pushing Boundaries with Microfluidics and Lab-on-a-Chip Technologies
Let’s talk about microfluidics. If you’re not already familiar with this incredible field, you really should be. These are devices that precisely manipulate and analyze minuscule volumes of fluids—think picoleters or nanoliters—on chips often no bigger than a postage stamp. They’re at the very cutting edge of diagnostic and therapeutic applications, promising to revolutionize everything from rapid disease detection to personalized drug screening. And guess what? Micro moulding plays a pivotal, absolutely indispensable role in their development.
At the heart of any microfluidic device are intricate micro channels, reaction chambers, mixers, and pumps, all designed to guide and control fluid flow with exquisite precision. We’re talking about structures sometimes just a few microns wide, smaller than the diameter of a single red blood cell. Fabricating these labyrinthine networks, with their precise dimensions and smooth internal surfaces, is incredibly challenging. Imagine trying to consistently etch or machine channels that small. It’s a nightmare. But micro moulding, with its ability to replicate ultra-fine features from a master mould, creates these essential components with remarkable fidelity and reproducibility.
The precision offered by micro moulding ensures that these components function optimally. Flow rates must be exact, mixing efficient, and reaction volumes consistent. Any imperfection—a tiny burr, an inconsistent channel width, an air bubble—can utterly compromise the device’s accuracy and reliability. Think about a point-of-care diagnostic device designed to detect a viral infection from a single drop of blood. The sample must flow seamlessly through multiple chambers, mixing with reagents, undergoing reactions, and finally yielding a result. Micro moulding ensures the integrity of this entire fluidic pathway, leading to faster, more accurate diagnostics right at the patient’s bedside, often eliminating the need for complex lab equipment.
Beyond diagnostics, microfluidics is enabling ‘organ-on-a-chip’ technologies, where miniature human organs are recreated on a chip to test drug efficacy and toxicity, reducing reliance on animal testing. It’s a huge leap for pharmaceutical research. It’s also critical for advanced cell sorting, DNA sequencing platforms, and even miniature drug synthesis systems. In all these applications, the ability to consistently produce complex, functional microfluidic components at scale, which micro moulding provides, is the foundational enabler. Without it, these revolutionary technologies simply couldn’t exist in their current form, or at least not economically. It’s truly a testament to engineering ingenuity.
Navigating the Complexities: Challenges and Future Directions
While micro moulding is undoubtedly a technological marvel, it’s not without its intricate challenges. You can’t just throw any material into a micro mould and expect perfection, can you? Two of the most significant hurdles revolve around material selection and the incredibly demanding process control required. Let’s delve into these a bit.
Material Selection: A Delicate Balancing Act
First, there’s the material challenge. In the medical field, biocompatibility is paramount. Any material destined for implantation or even prolonged contact with the human body must not elicit adverse reactions, no inflammation, no toxicity, nothing. This narrows down the field of usable polymers considerably. Common choices include high-performance engineering plastics like PEEK (polyether ether ketone), which offers exceptional strength and chemical resistance, or various grades of silicone, known for their flexibility and inertness. Then there are the aforementioned bio-resorbable polymers like PLA (polylactic acid) and PGA (polyglycolic acid), which degrade naturally over time.
However, working with these materials at a micro scale adds another layer of complexity. Their rheological properties – how they flow when molten – become incredibly critical. Some highly viscous polymers are difficult to inject into tiny mould cavities without excessive pressure, which can damage delicate mould features. Others might degrade under the shear forces encountered during injection. Furthermore, the thermal stability and degradation temperatures are incredibly sensitive. Overheat them, even slightly, and you compromise their integrity and performance. So, selecting the right material isn’t just about its properties in the final device; it’s about how it behaves during the moulding process itself. It’s a delicate balancing act, one that requires deep expertise.
Meticulous Process Control: The Art of the Invisible
Then comes process control. This isn’t your grandfather’s injection moulding. The sensitivity of these materials, combined with the minuscule scale of the components, demands an almost obsessive level of control over every single parameter. We’re talking about micro-adjustments in temperature profiles across different zones of the barrel and mould, precise control over injection speeds and pressures down to milliseconds, and incredibly accurate holding times and cooling rates. Even slight fluctuations in ambient temperature or humidity in the moulding facility can impact part quality when you’re working at these scales.
How do moulders achieve this? Through highly sophisticated, closed-loop control systems. These systems use an array of advanced sensors – think pressure transducers in the mould cavity, infrared sensors monitoring surface temperatures, and high-speed cameras – to provide real-time feedback. This data then feeds into algorithms that adjust machine parameters on the fly, ensuring consistent conditions throughout the entire moulding cycle. Many advanced facilities also leverage sophisticated simulation software to predict material flow and cooling behaviour even before a mould is cut, saving immense time and cost.
The Cost of Excellence and Quality Assurance
Another significant challenge, one that often comes up in conversations with industry colleagues, is the upfront cost. Micro moulding tools are incredibly expensive. Crafting a mould with features measured in microns requires specialist toolmakers, state-of-the-art machining equipment like micro-EDM (Electrical Discharge Machining) or laser ablation, and rigorous validation. But while the initial investment might be substantial, the return on investment comes from the ability to produce millions of high-precision parts consistently, driving down per-unit costs in high-volume applications.
And how do you inspect something you can barely see? Quality assurance for micro-moulded parts is another frontier. Traditional visual inspection just won’t cut it. Manufacturers employ advanced techniques such as automated optical inspection (AOI) systems, which use high-resolution cameras and sophisticated image processing algorithms. Even micro-CT (computed tomography) scans are used for non-destructive, three-dimensional internal inspection, ensuring there are no hidden voids or defects. It’s a testament to how far metrology has come.
The Road Ahead: Future Directions and Uncharted Territory
As the demand for even more complex and miniaturized medical devices continues to surge, ongoing research and innovation in micro moulding techniques will be absolutely essential. So, what’s next for this fascinating field?
- Hybrid Manufacturing Approaches: Expect to see more integration of micro moulding with additive manufacturing (3D printing). Imagine a core structure created via 3D printing, then micro-moulded features added for extreme precision. This could unlock even greater geometric complexity.
- Smart Devices: We’ll see more direct integration of micro-sensors and even micro-actuators directly into moulded components. Think about a tiny implant that not only delivers a drug but also monitors physiological parameters in real-time and adjusts dosage accordingly.
- Personalized Medicine: Micro moulding is perfectly poised to support mass customization. Imagine patient-specific implants or drug delivery systems tailored to an individual’s unique anatomy or genetic profile. The precision and repeatability of micro moulding make this achievable.
- Beyond the Micron: How small can we go? Research is pushing into the nano-moulding realm, opening up possibilities for even finer surface textures, drug nanoparticles, and molecular-level interactions.
- AI and Machine Learning: The massive amount of data generated by those precise process controls will be leveraged by AI and machine learning algorithms to predict and optimize moulding parameters, further reducing defects and improving efficiency.
- Sustainability: The industry is increasingly focused on reducing waste. Innovations in material recycling, energy-efficient moulding processes, and even the use of more bio-based or recyclable polymers are gaining traction, making the process itself more environmentally conscious.
The Tiny Giant: Micro Moulding’s Enduring Impact
So, there you have it. Micro moulding stands squarely at the intersection of truly remarkable precision engineering and the boundless potential of medical innovation. Its unparalleled ability to produce miniature, incredibly complex components with such unwavering accuracy isn’t just revolutionizing the biomedical field; it’s fundamentally reshaping the patient experience. We’re getting devices that are not only more effective in their therapeutic and diagnostic capabilities but also, crucially, more attuned to the comfort and recovery needs of patients. You can see how this leads to better healthcare outcomes across the board.
As technology relentlessly marches forward, one thing is crystal clear: the role of micro moulding in medical applications is set to expand, probably in ways we can’t even fully imagine right now. It’s a tiny giant, isn’t it, opening up entirely new possibilities for treatment, for diagnosis, and ultimately, for human health. And frankly, that’s incredibly exciting to witness. It truly makes you optimistic for the future of medicine.
Given the upfront cost of micro-moulding tools, what strategies could smaller medical device companies employ to access this technology and leverage its benefits without prohibitive capital expenditure?
That’s a great question! Exploring partnerships with universities or research institutions that have micro-molding capabilities could be a viable path. Collaborative projects can provide access to technology and expertise while sharing costs. Another option is to explore government grants to assist with funding. It is good to reduce barriers to this technology.
Editor: MedTechNews.Uk
Thank you to our Sponsor Esdebe
The discussion of material selection highlights a critical aspect. How are advancements in bio-integrated electronics influencing the types of materials now being considered for micro-moulding in implantable devices?
That’s a really interesting point! The increasing focus on bio-integrated electronics is certainly driving material innovation. We’re seeing more research into flexible, biocompatible polymers that can conform to the body’s natural movements, as well as conductive materials for seamless integration with electronic components. This is a rapidly evolving area!
Editor: MedTechNews.Uk
Thank you to our Sponsor Esdebe
The advancements in implantable devices using biodegradable materials are fascinating. What are the key challenges in ensuring consistent degradation rates and mechanical properties of these micro-moulded components within the body’s dynamic environment?
That’s a really important area to consider. The dynamic environment does present a challenge! There’s a lot of research focused on material blends and surface treatments to fine-tune degradation. Modelling software is also improving, helping predict performance under varying physiological conditions. It’s a multi-faceted approach!
Editor: MedTechNews.Uk
Thank you to our Sponsor Esdebe
The discussion around material selection is fascinating, especially the balance between biocompatibility and rheological properties at the micro-scale. Are there any novel materials emerging that might overcome the limitations of current options, perhaps through innovative composite structures or surface modifications?
That’s an excellent question! The push for improved materials is constant. There’s promising research into stimuli-responsive polymers that change properties based on their environment. Combining these with advanced surface modifications could lead to devices with dynamic functionality and enhanced biocompatibility! The field is moving fast.
Editor: MedTechNews.Uk
Thank you to our Sponsor Esdebe
Micro-moulding sounds amazing! I wonder, with such precision, are we getting closer to building real-life “Fantastic Voyage” submarines? Maybe not shrink a whole sub, but targeted drug delivery on a cellular level? Now that’s a movie I’d watch… or maybe *be* in!
That’s a fantastic thought! The precision of micro-moulding certainly opens up possibilities for targeted drug delivery on a cellular level. While shrinking a whole submarine might still be science fiction, creating micro-devices for precise interventions is becoming increasingly real! Imagine the potential for personalised medicine!
Editor: MedTechNews.Uk
Thank you to our Sponsor Esdebe
Fascinating stuff! If micro-moulding can achieve tolerances thinner than a human hair, does that mean we’re about to enter an era of medical devices so small we’ll need a microscope to lose them in the operating room? Imagine the headlines: “Surgeon General warns of rogue micro-stents escaping into the wild!”