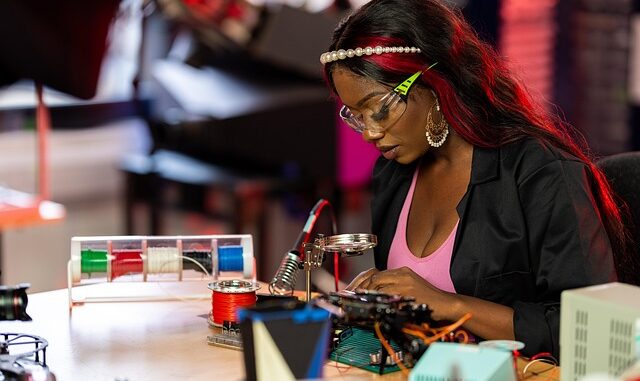
Advanced Sensor Technologies: Trends, Challenges, and Future Directions
Abstract
Sensor technology has undergone a remarkable evolution, transitioning from simple transducers to complex systems capable of providing real-time, high-resolution data across diverse applications. This report delves into the multifaceted landscape of advanced sensor technologies, examining their underlying principles, materials science, accuracy and reliability considerations, limitations, and emerging trends. We explore various sensor types, including those based on electrochemical, optical, microelectromechanical (MEMS), and quantum phenomena, highlighting their strengths and weaknesses. The report also addresses critical aspects such as biocompatibility in medical sensors, calibration techniques, advanced signal processing methodologies, and data security protocols, particularly relevant in networked sensor systems. Furthermore, we discuss the challenges associated with sensor miniaturization, power consumption, and environmental robustness. Finally, we present a forward-looking perspective on the future of sensor technology, exploring potential breakthroughs in areas such as flexible sensors, bio-integrated sensors, and the integration of artificial intelligence for enhanced sensor data analysis and interpretation. This report aims to provide a comprehensive overview of the current state-of-the-art and future directions in advanced sensor technology, targeting an expert audience familiar with the fundamental concepts.
1. Introduction
Sensors act as the interface between the physical world and electronic systems, converting various physical, chemical, or biological stimuli into measurable electrical signals. The information gleaned from these signals is crucial for applications ranging from industrial automation and environmental monitoring to healthcare diagnostics and consumer electronics. The demand for increasingly sophisticated and reliable sensors has fueled rapid innovation, leading to the development of advanced sensor technologies that offer improved sensitivity, selectivity, miniaturization, and power efficiency. This report provides a detailed exploration of these technologies, addressing their underlying principles, fabrication methods, performance characteristics, and future prospects.
2. Sensor Technologies: An Overview
Sensors can be broadly classified based on their operating principle and the physical quantity they measure. Several prominent sensor technologies are discussed below:
2.1 Electrochemical Sensors
Electrochemical sensors rely on the interaction between an analyte and an electrode surface to generate an electrical signal. These sensors are widely used in environmental monitoring (e.g., oxygen sensors, pH sensors), medical diagnostics (e.g., glucose sensors), and industrial process control. Common types of electrochemical sensors include potentiometric, amperometric, and conductometric sensors.
-
Potentiometric sensors measure the potential difference between two electrodes, which is related to the activity of a specific ion or molecule in the solution. The Nernst equation governs the relationship between the potential and the analyte concentration. Ion-selective electrodes (ISEs) are a prime example of potentiometric sensors.
-
Amperometric sensors measure the current generated by the oxidation or reduction of an analyte at a working electrode. The current is directly proportional to the analyte concentration under controlled potential conditions. Glucose sensors based on the enzymatic oxidation of glucose, catalyzed by glucose oxidase (GOx), are a well-known example.
-
Conductometric sensors measure the electrical conductivity of a solution, which changes with the concentration of ions or other conductive species. These sensors are commonly used for monitoring water quality and detecting the presence of pollutants.
The accuracy and reliability of electrochemical sensors are highly dependent on factors such as electrode material, electrolyte composition, temperature, and the presence of interfering species. Surface modification techniques, such as the deposition of nanomaterials or the immobilization of enzymes, are often employed to enhance the sensitivity and selectivity of these sensors.
2.2 Optical Sensors
Optical sensors utilize light to detect and measure various physical or chemical parameters. These sensors offer advantages such as high sensitivity, non-contact measurement, and the ability to perform remote sensing. Several types of optical sensors exist, including:
-
Absorption spectroscopy sensors: These sensors measure the absorption of light at specific wavelengths by an analyte. The Beer-Lambert law relates the absorbance to the analyte concentration and the path length of the light beam.
-
Fluorescence spectroscopy sensors: These sensors measure the emission of light by a fluorescent molecule after it has been excited by light at a shorter wavelength. Fluorescence-based sensors offer high sensitivity and selectivity and are widely used in bioanalysis and environmental monitoring.
-
Surface plasmon resonance (SPR) sensors: SPR sensors measure the changes in the refractive index at a metal surface due to the binding of molecules to the surface. SPR sensors are label-free and provide real-time detection of biomolecular interactions.
-
Fiber optic sensors: Fiber optic sensors use optical fibers to transmit light to and from the sensing element. These sensors are immune to electromagnetic interference and can be used in harsh environments. They can be used in a variety of configurations and many applications including monitoring structural integrity.
Advancements in light sources (e.g., LEDs, lasers), photodetectors (e.g., photodiodes, photomultiplier tubes), and optical materials have significantly improved the performance of optical sensors. Integration with microfluidic devices allows for miniaturized optical sensing systems with high throughput and reduced sample consumption.
2.3 Microelectromechanical Systems (MEMS) Sensors
MEMS sensors are miniaturized devices fabricated using microfabrication techniques. These sensors integrate mechanical and electrical components on a single chip, enabling the measurement of physical quantities such as pressure, acceleration, temperature, and flow rate. MEMS sensors offer advantages such as small size, low power consumption, and batch fabrication, making them suitable for a wide range of applications.
-
Pressure sensors: MEMS pressure sensors typically consist of a thin diaphragm that deflects under pressure. The deflection is measured using piezoresistive or capacitive sensing elements.
-
Accelerometers: MEMS accelerometers measure acceleration based on the inertial force acting on a proof mass. The displacement of the proof mass is measured using capacitive or piezoresistive sensing elements. They are common in smartphones.
-
Gyroscopes: MEMS gyroscopes measure angular velocity based on the Coriolis effect. These sensors are used in navigation systems and motion tracking devices.
-
Microphones: MEMS microphones use a thin diaphragm that vibrates in response to sound waves. The vibration is measured using capacitive sensing elements.
The performance of MEMS sensors is influenced by factors such as the design of the mechanical structure, the fabrication process, and the packaging. Advanced microfabrication techniques, such as deep reactive ion etching (DRIE) and surface micromachining, are used to create complex MEMS structures with high precision.
2.4 Quantum Sensors
Quantum sensors exploit quantum mechanical phenomena, such as superposition and entanglement, to achieve ultra-high sensitivity and precision in measurement. These sensors have the potential to revolutionize various fields, including medical imaging, materials science, and fundamental physics.
-
Atomic clocks: Atomic clocks use the resonant frequency of atoms to measure time with extreme accuracy. These clocks are used in GPS systems and telecommunications networks.
-
Quantum magnetometers: Quantum magnetometers measure magnetic fields with extremely high sensitivity. These sensors can be used for detecting weak magnetic signals from the brain or for detecting magnetic anomalies in the Earth’s crust.
-
Single-photon detectors: Single-photon detectors are capable of detecting individual photons with high efficiency. These detectors are used in quantum cryptography, quantum computing, and astronomical observations.
-
Nitrogen-vacancy (NV) center sensors: NV centers in diamond are point defects that exhibit unique quantum properties. NV centers can be used as nanoscale sensors for measuring magnetic fields, electric fields, temperature, and strain with high spatial resolution. They have shown excellent promise in medical imaging.
Quantum sensors are still in the early stages of development, and significant challenges remain in terms of scalability, cost, and integration with existing technologies. However, the potential benefits of these sensors are enormous, and ongoing research efforts are focused on overcoming these challenges.
3. Materials for Sensor Construction
The selection of appropriate materials is crucial for the performance and reliability of sensors. The choice of materials depends on the specific application and the operating principle of the sensor. Key considerations include sensitivity, selectivity, biocompatibility, chemical stability, and mechanical strength.
3.1 Conductive Materials
Conductive materials are used in various sensor applications, including electrodes, interconnects, and sensing elements. Common conductive materials include:
-
Metals: Gold, platinum, silver, and copper are widely used due to their high conductivity and chemical stability. However, some metals may be prone to oxidation or corrosion under certain conditions. They can be expensive to use.
-
Conductive polymers: Conductive polymers, such as polyaniline (PANI) and polypyrrole (PPy), offer advantages such as flexibility, low cost, and ease of processing. However, their conductivity is typically lower than that of metals.
-
Carbon-based materials: Carbon nanotubes (CNTs) and graphene exhibit excellent conductivity and mechanical strength. These materials are used in various sensor applications, including gas sensors, biosensors, and strain sensors.
3.2 Semiconductor Materials
Semiconductor materials are used in sensors based on electronic or optoelectronic principles. Common semiconductor materials include:
-
Silicon: Silicon is the most widely used semiconductor material due to its abundance, low cost, and well-established processing techniques. Silicon is used in MEMS sensors, photodiodes, and transistors.
-
Germanium: Germanium has a higher electron mobility than silicon, making it suitable for high-speed electronic devices. It is used in infrared detectors and high-frequency transistors.
-
III-V semiconductors: Gallium arsenide (GaAs), indium phosphide (InP), and gallium nitride (GaN) are used in high-frequency and optoelectronic devices due to their high electron mobility and direct bandgap. They are commonly found in LEDs and lasers.
-
Metal oxides: Metal oxides, such as zinc oxide (ZnO), titanium dioxide (TiO2), and tin oxide (SnO2), are used in gas sensors and photocatalytic applications. Their conductivity changes in response to the adsorption of gas molecules.
3.3 Dielectric Materials
Dielectric materials are used in capacitive sensors and insulators. Key properties include high dielectric constant, low dielectric loss, and high breakdown voltage. Common dielectric materials include:
-
Silicon dioxide (SiO2): SiO2 is a widely used dielectric material in microelectronics due to its excellent insulating properties and compatibility with silicon processing.
-
Silicon nitride (Si3N4): Si3N4 has a higher dielectric constant and better barrier properties than SiO2. It is used as a gate dielectric in transistors and as a passivation layer.
-
High-k dielectrics: High-k dielectrics, such as hafnium oxide (HfO2) and zirconium oxide (ZrO2), have a higher dielectric constant than SiO2, allowing for smaller and more efficient capacitors.
3.4 Biocompatible Materials
Biocompatible materials are used in medical sensors and implants to minimize adverse reactions with the biological environment. Key considerations include non-toxicity, non-immunogenicity, and resistance to degradation. Common biocompatible materials include:
-
Titanium and its alloys: Titanium and its alloys are widely used in implants due to their excellent biocompatibility and mechanical strength.
-
Stainless steel: Stainless steel is a cost-effective biocompatible material used in various medical devices. However, it may be prone to corrosion in certain environments.
-
Polymers: Polyethylene glycol (PEG), poly(lactic acid) (PLA), and poly(glycolic acid) (PGA) are biocompatible polymers used in drug delivery systems and tissue engineering scaffolds. They are used as protective coatings to reduce fouling on sensors.
-
Ceramics: Bioceramics, such as hydroxyapatite (HA) and tricalcium phosphate (TCP), are used in bone implants due to their osteoconductive properties.
4. Accuracy, Reliability, and Limitations
The accuracy and reliability of sensors are critical factors determining their suitability for specific applications. Accuracy refers to the closeness of a measurement to the true value, while reliability refers to the ability of a sensor to maintain its performance over time and under varying environmental conditions.
4.1 Factors Affecting Accuracy
Several factors can affect the accuracy of sensors, including:
-
Calibration errors: Calibration errors arise from inaccuracies in the calibration process or from drift in the sensor’s response over time. Regular calibration is essential to ensure accurate measurements.
-
Environmental factors: Temperature, humidity, pressure, and electromagnetic interference can affect the performance of sensors. Compensation techniques may be necessary to mitigate the effects of these factors.
-
Interfering species: The presence of interfering species can affect the selectivity of sensors, leading to inaccurate measurements. Selective membranes or filters can be used to minimize the effects of interfering species.
-
Noise: Noise in the sensor signal can reduce the accuracy of measurements. Signal processing techniques, such as filtering and averaging, can be used to reduce noise.
4.2 Factors Affecting Reliability
Factors affecting the reliability of sensors include:
-
Drift: Drift refers to the gradual change in the sensor’s response over time. Drift can be caused by aging of the sensor materials or by changes in the sensor’s environment.
-
Failure: Sensors can fail due to various reasons, such as mechanical damage, electrical overload, or chemical degradation. Redundancy and fault-tolerant design can improve the reliability of sensor systems.
-
Environmental conditions: Extreme temperatures, humidity, or corrosive environments can accelerate the degradation of sensors and reduce their reliability. Protective coatings and packaging can be used to improve the environmental robustness of sensors.
4.3 Limitations of Sensor Technologies
Each sensor technology has its own limitations. Some common limitations include:
-
Sensitivity: Some sensors may not be sensitive enough to detect low concentrations of the analyte of interest. This can be improved by optimising the design of the sensor.
-
Selectivity: Some sensors may be sensitive to multiple analytes, making it difficult to accurately measure the concentration of the analyte of interest. Techniques such as electrochemical impedance spectoscopy can be used to differentiate analytes.
-
Power consumption: Some sensors may consume a significant amount of power, limiting their use in battery-powered applications. Novel materials can be used to improve the power consumption of sensors.
-
Cost: The cost of some sensors may be prohibitive for certain applications. The use of cheaper materials can improve this. High volume production also reduces costs.
5. Signal Processing and Data Security
The raw signals from sensors often require processing to remove noise, compensate for environmental factors, and extract meaningful information. Furthermore, in networked sensor systems, data security is a critical concern.
5.1 Signal Processing Techniques
Various signal processing techniques are used to enhance the quality and accuracy of sensor data, including:
-
Filtering: Filters are used to remove noise from the sensor signal. Common types of filters include low-pass filters, high-pass filters, and band-pass filters.
-
Calibration: Calibration is used to compensate for errors in the sensor’s response. Calibration curves are generated by measuring the sensor’s output for known values of the measurand.
-
Compensation: Compensation is used to mitigate the effects of environmental factors, such as temperature and humidity. Compensation algorithms can be implemented in hardware or software.
-
Feature extraction: Feature extraction is used to identify relevant features in the sensor signal. These features can be used for classification, prediction, and other tasks. Machine learning algorithms can be very effective in feature extraction.
5.2 Data Security Protocols
Data security is essential in networked sensor systems to protect against unauthorized access, data tampering, and eavesdropping. Common data security protocols include:
-
Encryption: Encryption is used to protect the confidentiality of sensor data. Common encryption algorithms include AES and RSA.
-
Authentication: Authentication is used to verify the identity of sensor nodes and users. Common authentication methods include passwords, digital certificates, and biometric authentication.
-
Access control: Access control is used to restrict access to sensor data based on user roles and permissions. Role-based access control (RBAC) is a common access control model.
-
Data integrity: Data integrity mechanisms are used to detect data tampering. Hash functions and digital signatures can be used to ensure data integrity.
6. Future Trends and Directions
The field of sensor technology is constantly evolving, driven by the increasing demand for smarter, more efficient, and more versatile sensors. Some key future trends and directions include:
6.1 Flexible and Wearable Sensors
Flexible and wearable sensors are gaining increasing attention due to their potential for continuous and non-invasive monitoring of physiological parameters. These sensors are typically fabricated using flexible substrates, such as polymers or textiles, and can be integrated into clothing, bandages, or skin patches. Flexible sensors can be used for monitoring vital signs, detecting biomarkers in sweat, and tracking athletic performance.
6.2 Bio-Integrated Sensors
Bio-integrated sensors are designed to be implanted or integrated directly with biological tissues. These sensors offer the potential for real-time monitoring of physiological processes at the cellular or molecular level. Bio-integrated sensors require biocompatible materials and advanced microfabrication techniques to ensure long-term stability and functionality within the body.
6.3 AI-Enhanced Sensors
The integration of artificial intelligence (AI) with sensors enables advanced data analysis, pattern recognition, and predictive modeling. AI algorithms can be used to improve the accuracy, reliability, and sensitivity of sensors, as well as to extract meaningful information from complex sensor data. AI-enhanced sensors can be used for a wide range of applications, including medical diagnostics, environmental monitoring, and industrial automation.
6.4 Miniaturization and Nanotechnology
Ongoing efforts are focused on further miniaturizing sensors and incorporating nanotechnology to improve their performance and reduce their cost. Nanomaterials, such as nanoparticles, nanowires, and nanotubes, offer unique properties that can be exploited to enhance the sensitivity, selectivity, and response time of sensors. Miniaturized sensors can be integrated into portable devices and wireless sensor networks, enabling ubiquitous sensing.
7. Conclusion
Sensor technology is a rapidly evolving field that is poised to play an increasingly important role in various aspects of our lives. This report has provided a comprehensive overview of advanced sensor technologies, addressing their underlying principles, materials science, accuracy and reliability considerations, limitations, and emerging trends. The future of sensor technology is likely to be shaped by advancements in materials science, microfabrication techniques, AI, and nanotechnology, leading to the development of smarter, more efficient, and more versatile sensors. These sensors will enable new applications in fields such as healthcare, environmental monitoring, industrial automation, and consumer electronics, improving our understanding of the world around us and enhancing our quality of life.
References
- Datskos, P. G., Rajic, S., & Sepaniak, M. J. (2004). Carbon nanotube resonant structures as chemical and biological sensors. Sensors and Actuators B: Chemical, 99(1), 42-47.
- Turner, A. P. F. (2013). Biosensors: sense and sensibility. Chemical Society Reviews, 42(8), 3184-3196.
- Ewing, A. G. (2018). Instrumental methods of chemical analysis. John Wiley & Sons.
- Poole, C. P., & Owens, F. J. (2003). Introduction to nanotechnology. John Wiley & Sons.
- Janata, J. (2009). Principles of chemical sensors. Springer.
- Lynch, I., & Dawson, K. A. (2008). Protein–nanoparticle interactions. Nano Today, 3(1-2), 40-47.
- Hu, J., O’Connell, M. J., Yan, Y., Curlovic, L., Hong, W., & Lieber, C. M. (2003). Chemistry and physics of nanoscale materials: Single-walled carbon nanotube devices. Nature, 426(6964), 395-399.
- Rogers, J. A., Someya, T., & Huang, Y. (2010). Materials and mechanics for stretchable electronics. Science, 327(5973), 1603-1607.
- Kim, D. H., Lu, N., Ma, R., Kim, Y. S., Kim, R. H., Wang, S., … & Huang, Y. (2011). Epidermal electronics. Science, 333(6044), 838-843.
- Schwartz, D. K. (2003). Surface plasmon resonance bioassays. Surface Science Reports, 49(1-6), 1-70.
- Vettese, C., & De Micheli, G. (2017). Machine learning in biosensors. ACS sensors, 2(12), 1815-1828.
- Degiron, A., & De Lustrac, A. (2023). Introduction to Near-Field Optics. Cambridge University Press.
Given the discussion on sensor limitations, could the increasing reliance on AI for data processing inadvertently introduce new vulnerabilities or biases in sensor readings that might compromise overall accuracy?
That’s a great point! As we integrate AI for sensor data processing, we need to be aware of potential biases creeping in. AI models are trained on data, and if that data isn’t representative, the AI could skew the readings. Continuous validation and diverse datasets are key to mitigating this. Thanks for highlighting this important consideration!
Editor: MedTechNews.Uk
Thank you to our Sponsor Esdebe
Quantum sensors tickling your fancy? Wait until they’re seamlessly integrated with AI. Imagine nanoscale MRI with single-cell resolution. Diagnosing cancer before it even *thinks* about forming. I need to lie down.
That’s an exciting vision! The potential for AI-enhanced quantum sensors in early disease detection is truly mind-blowing. Thinking about preventative diagnostics at that level sparks so many possibilities. It’s a complex challenge, but the potential impact on healthcare makes it a path worth pursuing. Thanks for sharing this perspective!
Editor: MedTechNews.Uk
Thank you to our Sponsor Esdebe
The report highlights the importance of biocompatible materials for bio-integrated sensors. How do you see the regulatory landscape evolving to support the rapid development and deployment of these sensors, particularly regarding long-term safety and efficacy?
That’s a crucial question! I anticipate increased collaboration between regulatory bodies and researchers to establish clear guidelines for biocompatibility testing and long-term monitoring. Adaptive regulatory frameworks that evolve alongside the technology will be essential to foster innovation while safeguarding public health. Staged approvals based on risk could be an option.
Editor: MedTechNews.Uk
Thank you to our Sponsor Esdebe
Quantum sensors? Fantastic! Now, who’s volunteering to be the first human guinea pig for NV-center-enhanced medical imaging? Asking for a friend… who may or may not be a sentient AI.