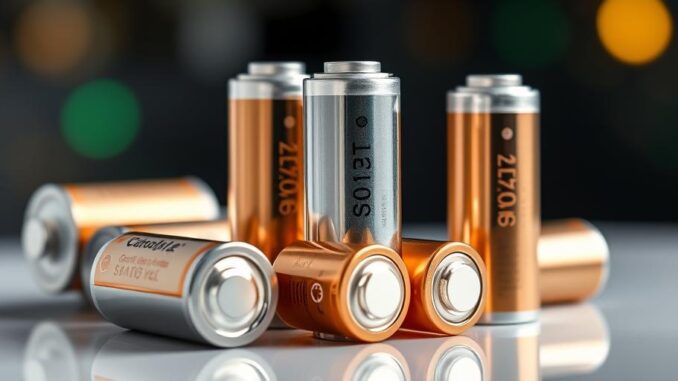
Advancements and Challenges in Cathode Materials for Lithium-Ion Batteries: A Comprehensive Review
Abstract
Lithium-ion batteries (LIBs) have revolutionized portable electronics, electric vehicles (EVs), and energy storage systems (ESS). The performance of LIBs, particularly energy density, power density, cycle life, and safety, is critically dependent on the cathode material. This review provides a comprehensive overview of the current landscape of cathode materials, encompassing layered oxides (NMC, NCA), polyanionic compounds (LFP, LVP), and spinel structures (LMO), highlighting their advantages, limitations, and degradation mechanisms. We delve into the intricate degradation pathways associated with each material class, including structural transformations, surface reactivity, metal dissolution, and electrolyte decomposition. Furthermore, this report scrutinizes the impact of electrolyte composition and operating conditions (temperature, voltage, current density) on cathode performance and stability. Finally, we explore cutting-edge mitigation strategies aimed at enhancing cathode stability, including surface coatings, elemental doping, electrolyte additives, and advanced cell designs. The review concludes with a discussion on future research directions and emerging trends in cathode material development, emphasizing the pursuit of high-energy, long-life, and safe LIBs for next-generation applications.
1. Introduction
The lithium-ion battery (LIB) has emerged as the dominant energy storage technology, powering a wide array of applications from smartphones to electric vehicles and grid-scale energy storage [1]. This widespread adoption is primarily attributed to their high energy density, power density, and relatively long cycle life compared to other battery technologies. However, increasing demands for even higher performance, improved safety, and reduced cost necessitate continuous innovation in all aspects of LIB technology, particularly in the realm of cathode materials.
The cathode material, responsible for lithium-ion intercalation and deintercalation during battery operation, plays a crucial role in determining the overall performance of the LIB [2]. The cathode material directly impacts the cell voltage, energy density, power density, cycle life, and safety characteristics. Therefore, the selection and optimization of cathode materials are paramount for tailoring LIB performance to specific applications.
This review aims to provide a comprehensive overview of the current state-of-the-art in cathode materials for LIBs. We will explore the key material classes, including layered oxides, polyanionic compounds, and spinel structures, dissecting their advantages, limitations, and intricate degradation mechanisms. Furthermore, we will analyze the influence of electrolyte composition and operating conditions on cathode stability. Finally, we will examine a range of mitigation strategies designed to enhance cathode stability and prevent performance degradation, paving the way for the development of next-generation LIBs.
2. Cathode Material Classes: Composition, Structure, and Properties
Cathode materials can be broadly categorized into three major classes: layered oxides, polyanionic compounds, and spinel structures. Each class exhibits distinct structural features, electrochemical properties, and performance characteristics.
2.1 Layered Oxides
Layered oxides, represented by the general formula LiMO2 (where M represents one or more transition metals), are characterized by a layered structure where lithium ions and transition metal ions occupy alternating layers [3]. These materials offer high theoretical capacities and relatively high operating voltages, making them attractive for high-energy-density applications. The most prominent layered oxides include lithium cobalt oxide (LiCoO2), lithium nickel manganese cobalt oxide (LiNixMnyCozO2, NMC), and lithium nickel cobalt aluminum oxide (LiNixCoyAlzO2, NCA).
-
Lithium Cobalt Oxide (LiCoO2): LiCoO2 was the first commercially successful cathode material and remains widely used in portable electronics due to its high energy density and ease of synthesis [4]. However, its high cost, toxicity of cobalt, and limited cycle life due to structural instability at high voltages restrict its use in large-scale applications like EVs.
-
Lithium Nickel Manganese Cobalt Oxide (NMC): NMC materials, with their tunable composition of nickel, manganese, and cobalt, offer a balance of high energy density, good power density, and improved safety compared to LiCoO2 [5]. The nickel content contributes to high capacity, manganese enhances structural stability, and cobalt improves rate capability. NMC materials with varying ratios of nickel, manganese, and cobalt (e.g., NMC111, NMC532, NMC622, NMC811) are tailored for specific applications. Higher nickel content NMCs (e.g., NMC811) offer higher energy density but are more prone to degradation and thermal runaway.
-
Lithium Nickel Cobalt Aluminum Oxide (NCA): NCA materials, particularly LiNi0.8Co0.15Al0.05O2, exhibit high energy density and good rate capability [6]. They are commonly used in high-performance EV batteries. However, NCA materials also suffer from poor thermal stability and require careful management to ensure safety.
2.2 Polyanionic Compounds
Polyanionic compounds, such as lithium iron phosphate (LiFePO4, LFP) and lithium vanadium phosphate (Li3V2(PO4)3, LVP), are characterized by the presence of strongly covalent polyanionic groups (e.g., PO43-, SO42-) in their structure [7]. These materials offer excellent thermal stability, long cycle life, and high safety due to the strong covalent bonding within the polyanionic framework. However, they typically exhibit lower energy density compared to layered oxides due to their lower operating voltage and theoretical capacity.
-
Lithium Iron Phosphate (LiFePO4): LFP is a widely used cathode material in EVs and ESS due to its inherent safety, long cycle life, and low cost [8]. Its olivine structure provides excellent thermal stability and resistance to structural degradation. However, LFP suffers from low electronic conductivity, which limits its rate capability. Various strategies, such as carbon coating and particle size reduction, have been employed to enhance its conductivity.
-
Lithium Vanadium Phosphate (Li3V2(PO4)3): LVP materials offer higher energy density and rate capability compared to LFP due to the higher redox potential of vanadium [9]. However, they are more expensive and exhibit lower cycle life than LFP.
2.3 Spinel Structures
Spinel structures, such as lithium manganese oxide (LiMn2O4, LMO), are characterized by a three-dimensional framework that provides excellent structural stability and high power density [10]. LMO is widely used in power tools and hybrid electric vehicles (HEVs) due to its low cost, high abundance of manganese, and good rate capability. However, LMO suffers from capacity fading at elevated temperatures due to manganese dissolution.
3. Degradation Mechanisms in Cathode Materials
The performance of LIBs degrades over time due to various degradation mechanisms affecting the cathode material. These mechanisms can be broadly categorized into structural degradation, surface degradation, and electrolyte decomposition.
3.1 Structural Degradation
Structural degradation involves changes in the crystal structure of the cathode material, leading to capacity fading and impedance increase [11]. These changes can be induced by lithium-ion intercalation/deintercalation, high-voltage operation, and elevated temperatures.
-
Phase Transformations: Layered oxides, particularly NMC and NCA materials, can undergo phase transformations during cycling, leading to structural instability and capacity fading [12]. For example, at high states of charge (SOC), the layered structure can transform to a spinel-like structure, which hinders lithium-ion diffusion and reduces capacity.
-
Microcrack Formation: Repeated lithium-ion intercalation/deintercalation can induce stress and strain within the cathode particles, leading to microcrack formation [13]. These microcracks increase the surface area exposed to the electrolyte, accelerating electrolyte decomposition and metal dissolution.
-
Metal Cation Mixing: In layered oxides, metal cation mixing, where transition metal ions occupy lithium sites, can occur during cycling, hindering lithium-ion diffusion and reducing capacity [14]. This is particularly problematic in nickel-rich NMC materials.
3.2 Surface Degradation
Surface degradation involves chemical and electrochemical reactions at the cathode-electrolyte interface (CEI), leading to the formation of a surface layer that impedes lithium-ion transport and accelerates electrolyte decomposition [15].
-
Electrolyte Decomposition: The electrolyte can decompose at the cathode surface, forming a resistive layer that increases impedance and reduces capacity [16]. This decomposition is accelerated at high voltages and elevated temperatures.
-
Metal Dissolution: Transition metal ions can dissolve from the cathode material into the electrolyte, leading to capacity fading and reduced cycle life [17]. This is particularly problematic for manganese-containing materials (e.g., LMO, NMC) in acidic environments. Dissolved metal ions can migrate to the anode and deposit, causing a further reduction in cell capacity and increased impedance.
-
Surface Reconstruction: The surface of the cathode material can undergo reconstruction during cycling, forming a disordered layer that hinders lithium-ion transport and accelerates electrolyte decomposition [18].
3.3 Electrolyte Decomposition
The electrolyte plays a crucial role in the performance and stability of LIBs. Electrolyte decomposition, particularly at the cathode, can lead to the formation of resistive layers, gas generation, and accelerated capacity fading [19].
-
Oxidation of Electrolyte: At high voltages, the electrolyte can be oxidized at the cathode surface, forming decomposition products that contribute to CEI formation and impedance increase [20].
-
Formation of HF: Trace amounts of water in the electrolyte can react with lithium salts (e.g., LiPF6) to form hydrofluoric acid (HF), which can corrode the cathode material and accelerate metal dissolution [21].
4. Influence of Electrolyte Composition and Operating Conditions
The electrolyte composition and operating conditions, such as temperature, voltage, and current density, significantly impact the performance and stability of cathode materials.
4.1 Electrolyte Composition
The electrolyte comprises a lithium salt dissolved in a solvent or mixture of solvents. The choice of lithium salt, solvent, and additives can significantly influence the electrochemical performance and stability of the battery.
-
Lithium Salts: Commonly used lithium salts include LiPF6, LiTFSI, LiBOB, and LiFSI. LiPF6 is the most widely used salt due to its good ionic conductivity and compatibility with many cathode materials [22]. However, it is susceptible to decomposition in the presence of water, forming HF. LiTFSI offers better thermal stability but can corrode aluminum current collectors at high voltages. LiBOB and LiFSI are promising alternatives with improved stability and conductivity.
-
Solvents: Common solvents include ethylene carbonate (EC), propylene carbonate (PC), dimethyl carbonate (DMC), and diethyl carbonate (DEC). EC provides good CEI formation and high ionic conductivity. PC offers good low-temperature performance but can cause graphite exfoliation at the anode. DMC and DEC are used to lower the electrolyte viscosity and improve rate capability.
-
Additives: Electrolyte additives are used to improve the performance and stability of LIBs by modifying the CEI, scavenging HF, and suppressing electrolyte decomposition [23]. Common additives include vinylene carbonate (VC), fluoroethylene carbonate (FEC), and lithium bis(oxalate)borate (LiBOB). VC and FEC promote the formation of a stable and ionically conductive CEI. LiBOB scavenges HF and improves the high-temperature performance of the battery.
4.2 Operating Conditions
-
Temperature: Elevated temperatures accelerate electrolyte decomposition, metal dissolution, and structural degradation of the cathode material [24]. Low temperatures can increase electrolyte viscosity and reduce lithium-ion diffusion, leading to reduced rate capability. Maintaining the battery within the optimal temperature range is crucial for maximizing performance and cycle life.
-
Voltage: High-voltage operation accelerates electrolyte oxidation and cathode material degradation [25]. Limiting the upper cutoff voltage can improve cycle life but reduces energy density. Developing high-voltage electrolytes and stable cathode materials is essential for achieving high-energy-density LIBs.
-
Current Density: High current densities can lead to polarization and increased heat generation, accelerating degradation mechanisms [26]. Optimizing the electrode design and electrolyte composition can improve rate capability and reduce polarization.
5. Mitigation Strategies for Enhancing Cathode Stability
Various strategies have been developed to enhance the stability of cathode materials and mitigate performance degradation. These strategies include surface coatings, elemental doping, electrolyte additives, and advanced cell designs.
5.1 Surface Coatings
Surface coatings involve applying a thin layer of protective material onto the cathode particles to improve their stability and prevent direct contact with the electrolyte [27]. Common coating materials include metal oxides (e.g., Al2O3, TiO2, ZrO2), metal fluorides (e.g., AlF3, LiF), and carbon.
-
Metal Oxide Coatings: Metal oxide coatings can act as a physical barrier to prevent electrolyte decomposition and metal dissolution [28]. They can also improve the structural stability of the cathode material. Al2O3 is a widely used coating material due to its chemical inertness and low cost.
-
Metal Fluoride Coatings: Metal fluoride coatings can scavenge HF and promote the formation of a stable and ionically conductive CEI [29]. AlF3 is a common fluoride coating material.
-
Carbon Coatings: Carbon coatings can improve the electronic conductivity of the cathode material and enhance its rate capability [30]. They can also protect the cathode surface from electrolyte decomposition.
5.2 Elemental Doping
Elemental doping involves substituting a small amount of one element for another in the cathode material lattice to improve its structural stability and electrochemical properties [31]. Common dopants include aluminum, magnesium, titanium, and fluorine.
-
Aluminum Doping: Aluminum doping can improve the structural stability of layered oxides and reduce metal dissolution [32].
-
Magnesium Doping: Magnesium doping can enhance the rate capability and cycle life of spinel LMO materials [33].
-
Titanium Doping: Titanium doping can improve the electronic conductivity and lithium-ion diffusion of LFP materials [34].
5.3 Electrolyte Additives
Electrolyte additives, as discussed in section 4.1, play a critical role in modifying the CEI, scavenging HF, and suppressing electrolyte decomposition. The judicious selection of additives can significantly improve the performance and stability of LIBs.
5.4 Advanced Cell Designs
Advanced cell designs, such as solid-state batteries and lithium-sulfur batteries, offer the potential to overcome the limitations of conventional LIBs and achieve higher energy density and improved safety [35].
-
Solid-State Batteries: Solid-state batteries utilize a solid electrolyte instead of a liquid electrolyte, eliminating the risk of electrolyte leakage and improving safety [36]. They also enable the use of high-voltage cathode materials and lithium metal anodes, leading to higher energy density.
-
Lithium-Sulfur Batteries: Lithium-sulfur batteries offer significantly higher theoretical energy density compared to LIBs [37]. However, they suffer from poor cycle life due to polysulfide dissolution. Developing strategies to suppress polysulfide dissolution is crucial for realizing the full potential of lithium-sulfur batteries.
6. Future Directions and Emerging Trends
Research and development in cathode materials are continuously evolving, driven by the increasing demand for high-performance, long-life, and safe LIBs. Future research directions and emerging trends include:
-
High-Nickel NMC and NCA Materials: Further increasing the nickel content in NMC and NCA materials to achieve even higher energy density is a key research focus [38]. However, this requires addressing the challenges of structural instability and thermal runaway.
-
Cobalt-Free Cathode Materials: Reducing or eliminating cobalt from cathode materials is desirable due to its high cost, limited availability, and ethical concerns [39]. Exploring alternative cathode materials, such as manganese-rich NMC and lithium-rich layered oxides, is a promising approach.
-
Solid-State Electrolytes: The development of stable and high-ionic-conductivity solid-state electrolytes is crucial for enabling solid-state batteries [40]. Both inorganic and polymer-based solid electrolytes are being actively researched.
-
Advanced Characterization Techniques: Employing advanced characterization techniques, such as in-situ and operando techniques, to gain a deeper understanding of the degradation mechanisms in cathode materials is essential for developing effective mitigation strategies [41].
-
Artificial Intelligence and Machine Learning: Utilizing artificial intelligence (AI) and machine learning (ML) techniques to accelerate the discovery and optimization of cathode materials is a growing trend [42]. AI/ML can be used to predict the performance of new materials, optimize synthesis parameters, and analyze experimental data.
7. Conclusion
Cathode materials are at the heart of lithium-ion battery technology, determining their energy density, power density, cycle life, and safety. This review has provided a comprehensive overview of the current landscape of cathode materials, encompassing layered oxides, polyanionic compounds, and spinel structures, highlighting their advantages, limitations, and degradation mechanisms. We have also examined the influence of electrolyte composition and operating conditions on cathode stability and explored a range of mitigation strategies aimed at enhancing cathode stability and preventing performance degradation. The pursuit of high-energy, long-life, and safe LIBs necessitates continuous innovation in cathode material development. Future research directions, including high-nickel NMC and NCA materials, cobalt-free cathode materials, solid-state electrolytes, advanced characterization techniques, and AI/ML-driven material discovery, hold the key to unlocking the full potential of LIB technology for next-generation applications.
References
[1] Goodenough, J. B., & Park, K. S. (2013). The Li-Ion Rechargeable Battery: A Perspective. Journal of the American Chemical Society, 135(4), 1167-1176.
[2] Whittingham, M. S. (2004). Lithium batteries and cathode materials. Chemical Reviews, 104(10), 4271-4302.
[3] Tarascon, J. M., & Armand, M. (2001). Issues and challenges facing rechargeable lithium batteries. Nature, 414(6861), 359-367.
[4] Mizushima, K., Jones, P. C., Wiseman, P. J., & Goodenough, J. B. (1980). LixCoO2 (0≤ x ≤ 1): A new cathode material for batteries of high energy density. Materials Research Bulletin, 15(6), 783-789.
[5] Liu, W., Oh, P., Liu, X., Lee, J. Y., Cho, J., & Yao, H. (2015). Overcharge behavior of Ni-rich layered oxide cathode materials: a comprehensive study. Advanced Energy Materials, 5(2), 1401882.
[6] Jung, S. K., Gwon, H., Hong, J., Park, K. Y., Kim, Y. J., & Park, J. K. (2015). Understanding the degradation mechanisms of LiNi0.8Co0.15Al0.05O2 cathode material in lithium-ion batteries. Energy & Environmental Science, 8(7), 2301-2311.
[7] Goodenough, J. B. (2007). Electrochemical energy storage in solids. Solid State Ionics, 178(17-18), 1319-1329.
[8] Padhi, A. K., Nanjundaswamy, K. S., & Goodenough, J. B. (1997). Phospho-olivines as positive-electrode materials for rechargeable lithium batteries. Journal of the Electrochemical Society, 144(4), 1188-1194.
[9] Li, G., Azhar, A., Wang, X., & Manthiram, A. (2015). High-performance Li3V2(PO4)3-based composites as cathode materials for Li-ion batteries. Journal of Materials Chemistry A, 3(20), 10815-10822.
[10] Thackeray, M. M. (1997). Spinel electrodes for lithium-ion batteries. Materials Science and Engineering: B, 41(1-3), 301-309.
[11] Chen, Z., Liu, Z., & Shen, X. (2017). Structural and chemical degradation of cathode materials in lithium-ion batteries: a review. Journal of Power Sources, 360, 406-421.
[12] Ryu, H. H., Park, J. K., Jung, S. K., Hong, S. T., & Park, J. W. (2011). Capacity fading mechanism of Li[Ni1/3Co1/3Mn1/3]O2 cathode material for lithium-ion batteries. Electrochimica Acta, 56(22), 7987-7992.
[13] Chiang, Y. M., Birnbaum, D., & Yet, K. Y. (2008). Materials science of lithium batteries. MRS bulletin, 33(07), 752-756.
[14] Kang, S. H., Lee, S. M., & Cho, J. (2009). Structural and electrochemical characteristics of Li[NixCoyMnz]O2 (x+ y+ z= 1) cathode materials with different compositions. Journal of the Electrochemical Society, 156(6), A461-A467.
[15] Verma, P., Maire, P., & Novák, P. (2010). A review of the formation and properties of the solid electrolyte interphase (SEI) on lithium-ion batteries. Electrochimica Acta, 55(22), 6332-6341.
[16] Peled, E. (1979). The electrochemical behavior of alkali and alkaline earth metals in nonaqueous electrolyte solutions. I. Lithium. Journal of the Electrochemical Society, 126(12), 2047-2051.
[17] Zhang, S. S. (2006). A review on electrolyte additives for lithium-ion batteries. Journal of Power Sources, 162(2), 1379-1394.
[18] Gallagher, K. G., Goebel, W., Coffey, K. R., Parkinson, D. Y., & Persson, K. A. (2016). Reversible and irreversible mechanisms of lithium-ion battery degradation. Accounts of Chemical Research, 49(9), 2093-2101.
[19] Xu, K. (2004). Nonaqueous liquid electrolytes for lithium-based rechargeable batteries. Chemical Reviews, 104(10), 4303-4418.
[20] Balbuena, P. B., & Wang, Y. (2004). Lithium-ion battery electrolytes. Solid State Ionics, 169(1-4), 21-40.
[21] Smart, M. C., Ratnakumar, B. V., & Surampudi, S. (1999). Electrochemical performance of lithium-ion cells at low temperatures. Journal of the Electrochemical Society, 146(2), 486-492.
[22] Xu, K. (2014). Electrolytes and electrolyte additives for lithium-ion batteries: Recent progress and perspective. Journal of Power Sources, 260, 316-328.
[23] Jung, R., Metzger, M., Maglia, F., Stinner, C., Gasteiger, H. A., & Loffler, T. (2015). Oxygen release and its effect on the cycling stability of LiNixMnyCozO2 (x + y + z = 1) positive electrode materials for lithium-ion batteries. Journal of the Electrochemical Society, 162(7), A1036-A1046.
[24] Waldmann, T., Wilka, M., Kasper, M., Fleischhammer, M., & Wohlfahrt-Mehrens, M. (2014). Aging mechanisms in lithium-ion batteries. Journal of Power Sources, 262, 129-149.
[25] Kasavajjula, U., Wang, C., & Appleby, A. J. (2007). Nano-and bulk-structured LiMn2O4 for lithium-ion batteries: A review. Journal of Power Sources, 163(2), 1003-1039.
[26] Arora, P., & Zhang, Z. (2004). Battery separators. Chemical Reviews, 104(10), 4419-4462.
[27] Cho, J., Kim, T. H., & Park, B. (2009). Coating as effective and facile approach for improving electro chemical, thermal, and structural properties of lithium transition metal oxide cathode materials. Journal of Materials Chemistry, 19(16), 2257-2267.
[28] Sun, Y. K. (2005). Synthesis and electrochemical behavior of surface-modified LiCoO2 cathode materials for lithium-ion batteries. Journal of Power Sources, 146(1-2), 44-48.
[29] Li, W., Manthiram, A., & Goodenough, J. B. (1997). LiF coating on LiMn2O4 spinel cathodes for lithium-ion batteries. Electrochemical and Solid-State Letters, 1(3), 157-159.
[30] Zhang, H., Xu, W., & Xue, G. (2010). Carbon-coated LiFePO4 as cathode material for high power lithium ion batteries. Journal of Power Sources, 195(5), 1350-1353.
[31] Manthiram, A., & Kim, J. (2010). Structural and electrochemical characterization of Li1+xMn2−xO4 spinels for lithium-ion batteries. Journal of the Electrochemical Society, 157(5), A580-A586.
[32] Myung, S. T., & Sun, Y. K. (2011). Lithium-rich layered oxide materials for high-energy lithium-ion batteries: A review. Journal of Materials Chemistry, 21(25), 9873-9887.
[33] Song, S. W., Lim, S. M., Kim, J. H., Kim, H. S., Yoon, W. Y., & Kim, D. H. (2007). Effect of Mg doping on the electrochemical performance of LiMn2O4 spinel as cathode material for lithium ion batteries. Journal of Power Sources, 174(2), 735-738.
[34] Chung, S. Y., Bloking, J. T., & Chiang, Y. M. (2002). Electronically conductive phospho-olivines as lithium storage electrodes. Nature Materials, 1(2), 123-128.
[35] Dunn, B., Kamath, H., & Tarascon, J. M. (2011). Electrical energy storage for the grid: a battery of choices. Science, 334(6058), 928-935.
[36] Janek, J., & Zeier, W. G. (2016). A solid future for battery electrolytes. Nature Materials, 15(4), 372-376.
[37] Manthiram, A., Fu, Y., Chung, S. H., Zu, C., & Kumar, A. (2014). Rechargeable lithium–sulfur batteries: Recent advances and remaining challenges. Chemical Reviews, 114(23), 11751-11787.
[38] Li, M., Lu, J., Chen, Z., & Amine, K. (2018). 30 years of lithium-ion batteries. Advanced Materials, 30(33), 1800561.
[39] Olivetti, E. A., Ceder, G., Gaustad, G. G., & Fu, X. (2017). Earth abundance of elements for rechargeable batteries. Joule, 1(2), 229-244.
[40] Zhao, Y., Daemen, L. L., Taylor, N. J., & Chi, M. (2022). Solid Electrolytes for Lithium Batteries: Progress, Challenges, and Future Directions. Advanced Energy Materials, 12(3), 2102877.
[41] McCloskey, B. D. (2015). Electrolyte decomposition in lithium-ion batteries. Journal of Physical Chemistry Letters, 6(22), 4497-4513.
[42] Sendek, A. D., Cubuk, E. D., Kikuchi, T., Himeda, T., Persson, K. A., & Aspuru-Guzik, A. (2017). Holistic computational structure screening of more than 12 000 candidates for solid-state Li-ion conductors. Energy & Environmental Science, 10(1), 306-320.
So, if we are tweaking these cathode materials to the nth degree, are we also looking at equally innovative manufacturing processes to keep costs down and production scalable? Asking for my wallet’s sake!
That’s a great point! Innovative manufacturing is absolutely crucial. Research into scalable and cost-effective production methods, like advanced synthesis techniques and optimized coating processes, is a key area of focus alongside material development. Bringing down costs is vital for widespread EV adoption!
Editor: MedTechNews.Uk
Thank you to our Sponsor Esdebe
This review comprehensively addresses degradation mechanisms. How might advanced characterization techniques like operando X-ray diffraction further refine our understanding of structural changes during battery cycling, particularly for high-nickel NMC materials?
That’s a fantastic question! Operando X-ray diffraction is indeed a powerful tool. Visualizing the structural changes in real-time during battery operation allows us to pinpoint the exact moments when degradation begins. By understanding this relationship, we can develop more targeted strategies for material stabilization and improved battery lifespan, especially for those tricky high-nickel materials. Thanks for sparking this discussion!
Editor: MedTechNews.Uk
Thank you to our Sponsor Esdebe
This is a valuable overview of the field. Considering the challenges around electrolyte decomposition, what are your thoughts on the potential of novel electrolyte additives, such as those forming robust solid electrolyte interphases, in extending the lifespan of high-nickel NMC cathodes?
Thanks for your insightful comment! Electrolyte additives are indeed a promising avenue. The ability of these additives to create stable, robust SEIs is a critical factor for long-term performance, especially in high-nickel NMC cathodes. Further research into additive chemistries and their interactions with cathode materials is essential for advancing LIB technology.
Editor: MedTechNews.Uk
Thank you to our Sponsor Esdebe
The discussion on advanced cell designs is fascinating. Solid-state batteries eliminating liquid electrolytes promise enhanced safety and energy density. What advancements in solid electrolyte materials are proving most effective in overcoming challenges like interfacial resistance and dendrite formation?